QRKの軸受けが出来ました。
左がオリジナル。右が僕の作った物。
オリジナルは、かなり硬いアルミ合金に穴を開けただけ。
僕のは、アルミケースの中に、砲金のスリーブを焼き嵌めした物。
で、今回はチョット懲りました。
砲金のスリーブ、上下で分かれているのです。
スリーブに応力の掛かるのは、上と下。
真ん中は殆ど応力が掛かりません。
だったら・・・・・・。
其処の部分にはスリーブを入れなかったのです。
面倒な事をしてなんで?
エーーー。実は内部に入るオイルの量を、確保したかったのですね。
中心にスリーブの肉厚分(2mm)の空間が出来ました。此処へタップリとオイルを確保する作戦です。
オイル量が増えれば、メンテサイクルも伸びます。
で、このスリーブ単に焼き嵌めしただけですと、アルミの収縮と同時にスリーブも押し縮められ、内径が小さく成ります。
今回の様に、上下分割ですと、上下のスリーブのセンターもズレます。
最初から其れを見込んでスリーブの内径は若干小さめに作って置き、焼き嵌め後、もう一度旋盤で内径をさらうのです。
こうしないと、良い軸受けは出来ません。
でも、懲り過ぎだなー・・・・。
QRKの改良を頼まれたのは良いのですが、なんせ個体差の多いターンテーブルです。
イエ、メーカーの保障精度では誤差内に収まっているんでしょうが・・・・。
自分でもターンテーブルを作っています。
許容誤差は結構シビア。
そんなのを作っていると、メーカー改造と言っても、同じ精度にしたくなって・・・(困った性格、汗)。
軸受けを作り直すのですが、軸受けの穴径、どの様にして測ります?
外径を正確に測るのはそんなに難しく有りません(と言っても他人の測定値は信用しませんが、笑)。
問題は穴径。測定器具は有りますが、測定の仕方でかなりの誤差が・・。
一番間違いの無い方法。ピンゲージ。要は穴径ピッタリのシャフトを作り其れを差し込むのです。
市販のピンゲージは1/100単位で売られていますが、無茶苦茶に高い。
で、今回はこんなのを・・・。
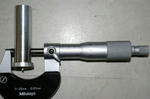
マイクロメーターで測ると15,69強。
で、QRKは・・?

略ドンピシャ。
オイオイ旋盤が有るんだから、簡単だろう。 ですか?
一般の旋盤(僕のも)、縦送りの目盛り、最小で0,025mm。
此れは半径ですから、直径にすると0,05mm。
つまり一目盛り(略1mm)ハンドルを回すと、工作物の直径は5/100mm変わってしまうのですね。
単にネジを切って有るシャフトを回すのですから、この精度が精一杯なんです。
じゃーどうやって?
ハイ、旋盤と仲良しに成るんです。
こいつはアルミの場合はこの程度送ると1/100削れるって体で覚えるしかないんです。
旋盤を導入した当時。この精度で仕上げるには数本作って1本取れるかどうか。
今日は一発で出来ました。
別に導入当時と変わった事はしていません。
旋盤と仲良くなっただけです。
あ、僕愛用の旋盤。ナント1970年製。
大阪万博の年です。
で、この年は僕にとっても大切な年。
高校を卒業し、田舎から東京に出てきた年なんです。
なんか、不思議なめぐり合わせです。
イエ、メーカーの保障精度では誤差内に収まっているんでしょうが・・・・。
自分でもターンテーブルを作っています。
許容誤差は結構シビア。
そんなのを作っていると、メーカー改造と言っても、同じ精度にしたくなって・・・(困った性格、汗)。
軸受けを作り直すのですが、軸受けの穴径、どの様にして測ります?
外径を正確に測るのはそんなに難しく有りません(と言っても他人の測定値は信用しませんが、笑)。
問題は穴径。測定器具は有りますが、測定の仕方でかなりの誤差が・・。
一番間違いの無い方法。ピンゲージ。要は穴径ピッタリのシャフトを作り其れを差し込むのです。
市販のピンゲージは1/100単位で売られていますが、無茶苦茶に高い。
で、今回はこんなのを・・・。
マイクロメーターで測ると15,69強。
で、QRKは・・?
略ドンピシャ。
オイオイ旋盤が有るんだから、簡単だろう。 ですか?
一般の旋盤(僕のも)、縦送りの目盛り、最小で0,025mm。
此れは半径ですから、直径にすると0,05mm。
つまり一目盛り(略1mm)ハンドルを回すと、工作物の直径は5/100mm変わってしまうのですね。
単にネジを切って有るシャフトを回すのですから、この精度が精一杯なんです。
じゃーどうやって?
ハイ、旋盤と仲良しに成るんです。
こいつはアルミの場合はこの程度送ると1/100削れるって体で覚えるしかないんです。
旋盤を導入した当時。この精度で仕上げるには数本作って1本取れるかどうか。
今日は一発で出来ました。
別に導入当時と変わった事はしていません。
旋盤と仲良くなっただけです。
あ、僕愛用の旋盤。ナント1970年製。
大阪万博の年です。
で、この年は僕にとっても大切な年。
高校を卒業し、田舎から東京に出てきた年なんです。
なんか、不思議なめぐり合わせです。
1本のアームはヤット神戸へ発送。
もう一本。こちらは持ち込みのQRKへの取り付けです。
僕のHPをしっかりと見ていられ、僕のQRKへのノウハウもシッカリとご存知。
其の改良も同時に施してと言うオーダーです。
懐かしいマイクロトラックのアームが付いています。
此れを取り外し、各部の寸法の確認です。
以前に改良を行ったQRKと寸法が同じ保障が有りませんから。
さて、どこから手を付けるか・・・・・・。
連続運転したギヤボックス内のオイルは汚れます。
ウォームギヤは歯同士が擦れあって運転。
その為、どうしても金属粉が発生するのです。
其の金属粉は、有る意味研磨剤。
オイルを排出すれば大多数は外へ出ますが、臍曲がりの金属粉は内部に・・・。
で、洗ってしまいましょう。
フラッシングオイル。
車のエンジン内をクリーニングするオイルです。
ベースは灯油ですが、灯油100%ですと、エンジンを痛めてしまうので、潤滑油も配合して有ります。
以前、僕の所でオイル交換をしたある車。
交換前にフラッシングをしました。
かなり痛んでいたらしい、入っていたオイル。
フラッシングオイルの方がメカノイズが少なくなり、僕は呆然(笑)。
エンジン内に入れてもOKな洗浄オイルですから、ギヤボックスなら絶対に平気。
早く気付けば、内部洗浄にアクリル板を外さないでも済んだのに・・・。
先日購入した、新しいガスケット。
十日程前に、内部クリーニングをしたギヤボックスに使い、大成功。
今回は紙パッキンを入れないで、液体ガスケットだけでの実験。
数日間、昼夜を問わず運転続行。
僕は其の間、旋盤でホーンの製作。

机の上に置かれたギヤボックス。
連続運転が効いて、ギヤ音も小さくなり絶好調。
前にも書きましたが、僕のギヤボックス3個目。
ウォームギヤと軸受けに長時間の慣らしが必要。って言ったら、僕の使っているのを持って行ってしまったお客様がいたんですね。
先日、内部クリーニングしたのは、かなり最初に作った物。ユーザーの使用時間は無茶長い。
良い耐久テストをしてもらった感じです(笑)。
クリーニングして、オイルを注入。シャフトを手で廻すと・・・・・・。
軽い。それでいてガタが無い。
もう、僕のギヤボックスは人には渡さないぞ。って心に誓った瞬間でした。
で、僕のギヤボックス。液体ガスケットだけでオイル漏れゼロ。
成功ですが、ガスケットの色が表から見えチョット恥ずかしい。
アクリルの上に何らかのカバーを付ければ・・・・・・。
十日程前に、内部クリーニングをしたギヤボックスに使い、大成功。
今回は紙パッキンを入れないで、液体ガスケットだけでの実験。
数日間、昼夜を問わず運転続行。
僕は其の間、旋盤でホーンの製作。
机の上に置かれたギヤボックス。
連続運転が効いて、ギヤ音も小さくなり絶好調。
前にも書きましたが、僕のギヤボックス3個目。
ウォームギヤと軸受けに長時間の慣らしが必要。って言ったら、僕の使っているのを持って行ってしまったお客様がいたんですね。
先日、内部クリーニングしたのは、かなり最初に作った物。ユーザーの使用時間は無茶長い。
良い耐久テストをしてもらった感じです(笑)。
クリーニングして、オイルを注入。シャフトを手で廻すと・・・・・・。
軽い。それでいてガタが無い。
もう、僕のギヤボックスは人には渡さないぞ。って心に誓った瞬間でした。
で、僕のギヤボックス。液体ガスケットだけでオイル漏れゼロ。
成功ですが、ガスケットの色が表から見えチョット恥ずかしい。
アクリルの上に何らかのカバーを付ければ・・・・・・。
本日の仕事。ギヤボックスのカップリングの交換。
マグネットカップリングです。
磁力で動力の伝達をしますので、入出力間に機械的な接続が無いんですね。
結果、細かな振動等を伝え難く成るのです。
最初付けた時、其れ成りに効果が有りました。
でも、長時間使ってきたら・・・・・・・。
モーターのベアリング音が気に成ってきたのです。まあ、其れだけカップリングの音が無く成った、と言う事でも有るのですが・・・・・。
このカップリング。産業用ですから細かな取説なんて付いて来ません。
もう一度、カップリングを外し細かく採寸。
要は、インナーとアウターのマグネットを最適位置にセットしたいのです。
軸上寸法が少々ずれても、カップリングは正常動作しますが、スラスト荷重を発生させてしまうのです。
其の荷重がベアリングノイズの原因と読みました。
キッチリ採寸したら1~2mm、モーター側へ深く差し込む必要が・・・。
調整の終わったギヤボックス。
勿論更に静かに。
どんな小さな事にもノウハウって有るんです。
今日、一生懸命頑張っている仕事。
何を作っているのでしょう?
鋭い方は、中に入っているコンデンサーでハハ~~~~ン。
えー、隣のギヤボックスを頼まれた方にこれも頼まれました。
僕のギヤボックス。33回転オンリーか45回転との2スピード。
今回のお客様。SP盤も愛用されているのです。
つまり78回転。
今のギヤボックスに78回転のプーリーを付けると、トンでもない大きさに成ります。
直径145mm強。
ギヤボックスの置く所が凄く制限されてしまいます。
糸の長さもかなりなものに・・・。
で、78回転用に別途にモーターを付ける事にしました。
ギヤ無しで、直接駆動です。
只、78回転ですとプーリーの直径も大きくなりますし、ターンテーブルの慣性モーメントも偉大に成りますので、十分いけます。
本当は4月末に納品の予定でした。
つまらない事故の為、ヤット完成間近に成りました。
さあ、もうちょい。
肩の不調で、得意の重量構造体の製作が滞っていました。
でも、ソロソロやりたい。此れを作んなきゃ僕じゃない(笑)。
写真のアルミ板(ブロックかも?)、厚みは30mm有ります。
うっかりバイクで買いに行って、帰りはよろよろ(実は更に40mmも買って来た、汗)。
買って来た侭では、周りの切断面はザラザラ。うっかり触ると手を切ります。
フライスで仕上げ、面取りをしてヤット安心して触れます。
なんか、お菓子かお寿司みたい。サンドイッチです。挟まれている青い物の正体はソルボセイン。衝撃吸収ゴムです。
厚みは5mm。硬度はハードをチョイス。
アンプの下に挟む場合は、あくまでも振動を伝えないのを最優先しますから、ソルボセインは必要最少量。
多過ぎると、振動を伝えてしまうのですね。
で、今回の使用では、横揺れ厳禁。
ソルボセインを、向かい合っている面全体に挟んで有ります。
4箇所に切って有るネジを使い、プラ足の取り付け。
で、何に使うのかと言いますと・・・・・。
ギヤボックスの台。
オイオイ、高過ぎちゃうだろうの声も聞こえますが・・・・。
一般に使用されている、1本アーム用のプレーヤーキャビ。
このキャビには高過ぎてしまいます。
今回取り付けるのはこのキャビ。
まだ僕のアームの無い時代に、沢山作ったキャビです。
当時はどうしてもアームが2~3本必要でした。
帯に短し、たすきに長しのアームしか無かったのですね。
僕のアームが出来てから、1本アームのキャビを使う方が多く成りました。
今回は其の時代に作ったキャビ用なのです。
最初は何か適当な木材を・・・・・。
なんて思っていましたが、どうせやるならとお客様からのご依頼でした。
ここまでやれば万全です。