試作機が巧く行ったギヤボックス。
早速注文が2台。
でも、試作機の侭での出荷は出来ません。
試作したからこそ、見えて来た問題点。
試作機には有って当たり前。
図面でどんなに頑張り、アイディアで頑張っても問題点は必ず出るものです。
その辺の修正をしないと、量産(そんなに作るのかな?)に掛かれません。
更に、図面を書いたばかりは、細かい所は頭に入っているので、少々簡略した図面でも作れますが、暫くぶりに受注、と成ると、図面を引いてから時間が経っているので、此処はどうだったかなー?
なんて成り易い。
要は、外注に出しても間違いの無い物が作れる図面を、書く必要が有るのです。
部品点数が多く、3次元での形状ですから、図面はしっかりと書かないと間違い易い。
今日明日の二日間で出来るかな?
BBSの方にチラッと書いておいたんだけど、誰も気付かないようで・・・・(その方が良かったりして、汗)。
実はギヤボックス、完成していました。
今掛かっているアンプのシャシを彫刻屋さんへ持って行くと・・・。
『今、仕事が無くて暇なんだよー。で、今がチャンスと工場の整理を始めてしまったんだよね。だから仕事に掛かれるのに一週間掛かるんだよ。』
彫刻屋さんの社長の言葉です。
何時もなら、持って行った翌日に出来てるのに・・・・・。
一週間空いてしまった。ギヤボックス作ろう。
でも、アンプのお客さんになんて言おう。其れでなくても納期が遅れているのに・・・・。
そんな状態でギヤボックスが出来たなんてアップできないし・・・・(悶々)。
で、昨日、アンプのお客様と電話。とても良い方で、遅れる事よりも良いアンプを御希望。ギヤボックスの件も話しちゃったし。
と言う事で、堂々とアップ出来ます(大汗)。
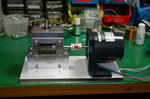
完成したギヤボックス。スケルトンなのがカッコいい(笑)。
オイルのシミに見えるのは液体ガスケット。バイクで使い慣れてます。
普段、『バイク屋さん』って言われているのをシッカリと実践。
なんせ、オイルフィラー(注入口)。オイルドレイン(排出口)。オイルブリザー(換気口)をちゃんと作ってますし、シャフトの出入口にはオイルシールまでキッチリと入れる始末。
バイクを弄っていて良かったー(全てバイク弄りで覚えたノウハウ)。
スケルトンにしたのには、ちゃんとした訳が有って、まずオイルの量の確認が楽(レベルゲージを作らないで済む)。
更にオイルの汚れが一目瞭然。
一番大事なのが、オイルの流れを確認できる事。本番では必要無いですが、試作機です。オイルがどの様に流れているかを確認したいし、オイルの粘度が適切かも知りたかったのです。
試運転開始。2時間でオイルは汚れてしまいました。スケルトン大成功。
ギヤのカタログにも、運転最初はオイルの汚れが酷いと書いて有りましたし。
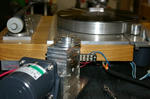
プレーヤーに接続。
何時ものレコードに針を下ろす。
音を伝えられないのが残念。
判ってもらえる事は、最初に聞いた友人。その場で発注して帰りました。
もう、戻れません。
実はギヤボックス、完成していました。
今掛かっているアンプのシャシを彫刻屋さんへ持って行くと・・・。
『今、仕事が無くて暇なんだよー。で、今がチャンスと工場の整理を始めてしまったんだよね。だから仕事に掛かれるのに一週間掛かるんだよ。』
彫刻屋さんの社長の言葉です。
何時もなら、持って行った翌日に出来てるのに・・・・・。
一週間空いてしまった。ギヤボックス作ろう。
でも、アンプのお客さんになんて言おう。其れでなくても納期が遅れているのに・・・・。
そんな状態でギヤボックスが出来たなんてアップできないし・・・・(悶々)。
で、昨日、アンプのお客様と電話。とても良い方で、遅れる事よりも良いアンプを御希望。ギヤボックスの件も話しちゃったし。
と言う事で、堂々とアップ出来ます(大汗)。
完成したギヤボックス。スケルトンなのがカッコいい(笑)。
オイルのシミに見えるのは液体ガスケット。バイクで使い慣れてます。
普段、『バイク屋さん』って言われているのをシッカリと実践。
なんせ、オイルフィラー(注入口)。オイルドレイン(排出口)。オイルブリザー(換気口)をちゃんと作ってますし、シャフトの出入口にはオイルシールまでキッチリと入れる始末。
バイクを弄っていて良かったー(全てバイク弄りで覚えたノウハウ)。
スケルトンにしたのには、ちゃんとした訳が有って、まずオイルの量の確認が楽(レベルゲージを作らないで済む)。
更にオイルの汚れが一目瞭然。
一番大事なのが、オイルの流れを確認できる事。本番では必要無いですが、試作機です。オイルがどの様に流れているかを確認したいし、オイルの粘度が適切かも知りたかったのです。
試運転開始。2時間でオイルは汚れてしまいました。スケルトン大成功。
ギヤのカタログにも、運転最初はオイルの汚れが酷いと書いて有りましたし。
プレーヤーに接続。
何時ものレコードに針を下ろす。
音を伝えられないのが残念。
判ってもらえる事は、最初に聞いた友人。その場で発注して帰りました。
もう、戻れません。
以前、アップしたウォームギヤ。
この類の物は、単にギヤとしての素材を提供しますから、貴方の使い方に合った形に改造してね。と言う物です。
早い話、シャフトとの連結も自分で考えてね。と言うギヤ。
産業機器用ですからいたって当然です。
で、早速改造。
上の写真と較べて違いが判りますか?
二箇所変わっています。
まず、シャフトとの連結の為に、横からネジ穴をあけています。M3を二箇所。
このネジ穴。シャフトに対して120°であけちゃうと、ネジが緩みやすい。90°であけるのが正解。
もう1つ。シャフトを通す穴径。6mmから8mmへ拡大。
こんなの簡単と思ったら、旋盤に詳しくない。
元の穴と角度、中心位置を狂わせないで開けるのには、かなりの注意を払わないと確実に狂います。
旋盤作業の肝。一度咥えた材料は、咥えなおさないで一気に切削が基本です。
一度穴の開いたものを、チャックに咥えなおしてセンターを合わせるのはかなり難しいのです。
色々工夫をして、センターをあわせ、ドリルで広げ、その後穴ぐりバイトで寸法を合わせます。
まだまだ、先は長い。
ギヤボックスの作業は、工具の入荷待ちで一時中断。
で、その間に出来る仕事。
プーリーの製作です。
丁度70Φの丸棒も有りましたし。
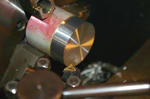
ギヤで1/10に減速しますので、プーリーの直径は10倍に成ります。
前回の実験で、音が良かったのはこの所為と予測。
と言うのは、プリ-径が大きいと、糸の掛かる長さが増えます。
結果、糸のスリップが少なくなり、負荷変動に強くなった為と踏んでます。
プーリーが大きくなると、作るのも楽(あまり言いたくない、汗)。
直径の許容誤差が大きくなるのです。
早い話0.1mm狂っても問題は全然出ません。
従来のプーリーでしたら大変な問題です。
旋盤仕事で0.1mm狂ってもOKと言うのは凄く楽。
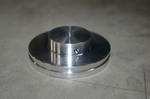
出来上がったプーリー。溝部の直径は65.8mm。
此れだけ大きいと、磨耗も殆どしないでしょうから、アルミで作りました。
で、その間に出来る仕事。
プーリーの製作です。
丁度70Φの丸棒も有りましたし。
ギヤで1/10に減速しますので、プーリーの直径は10倍に成ります。
前回の実験で、音が良かったのはこの所為と予測。
と言うのは、プリ-径が大きいと、糸の掛かる長さが増えます。
結果、糸のスリップが少なくなり、負荷変動に強くなった為と踏んでます。
プーリーが大きくなると、作るのも楽(あまり言いたくない、汗)。
直径の許容誤差が大きくなるのです。
早い話0.1mm狂っても問題は全然出ません。
従来のプーリーでしたら大変な問題です。
旋盤仕事で0.1mm狂ってもOKと言うのは凄く楽。
出来上がったプーリー。溝部の直径は65.8mm。
此れだけ大きいと、磨耗も殆どしないでしょうから、アルミで作りました。
簡単にギヤ駆動なんて言っちゃいましたが、色々と工夫が必要です。
まずギヤボックス。
平板の組み立て式が一番簡単ですが、軸受けの直線性を保障できません。
一番はキャスティングの削りだし。でも此れは量産が大前提。
僕の所の生産数量では、とても出来ない方法です。
機械強度を十分に稼がないと、ギヤ音も出易くなります。なんせレコードプレーヤー。SN比と言う項目、無視できません。
一番贅沢な方法。アルミブロックからの削りだしで作る事にしました。
此れならキャスティングに負けません。
と言って、一体でのくりぬきは不可能。2ピースでの製作です。
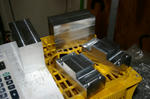
外寸を出したブロック。
切削する時に測る寸法は、平らな面から。兎に角ブロックの外寸と直角度が命です。
普段はノギスでの測定ですが、今回は基準寸法をマイクロメーターで測定。
ギヤの隙間を、メーカー指定値にする為の工夫です。
厚み50mmの板からの切削でしたが、買って来た板は0.3mm厚い。
此れも50mmピッタリに切削しました。
外寸を出すだけで略二日間。大変でしたが、此処で手を抜くと後々の精度が出ません。
さて此処から、軸受けの穴あけ。
で、頼んだロングドリルがまだ来ない。
アンプのシャシは出来てこないし、何しよう・・・・。
まずギヤボックス。
平板の組み立て式が一番簡単ですが、軸受けの直線性を保障できません。
一番はキャスティングの削りだし。でも此れは量産が大前提。
僕の所の生産数量では、とても出来ない方法です。
機械強度を十分に稼がないと、ギヤ音も出易くなります。なんせレコードプレーヤー。SN比と言う項目、無視できません。
一番贅沢な方法。アルミブロックからの削りだしで作る事にしました。
此れならキャスティングに負けません。
と言って、一体でのくりぬきは不可能。2ピースでの製作です。
外寸を出したブロック。
切削する時に測る寸法は、平らな面から。兎に角ブロックの外寸と直角度が命です。
普段はノギスでの測定ですが、今回は基準寸法をマイクロメーターで測定。
ギヤの隙間を、メーカー指定値にする為の工夫です。
厚み50mmの板からの切削でしたが、買って来た板は0.3mm厚い。
此れも50mmピッタリに切削しました。
外寸を出すだけで略二日間。大変でしたが、此処で手を抜くと後々の精度が出ません。
さて此処から、軸受けの穴あけ。
で、頼んだロングドリルがまだ来ない。
アンプのシャシは出来てこないし、何しよう・・・・。
此処に新しいモーターをアップしたら、反響大(汗)。
失敗は出来なくなった。有言実行は辛い。
で、下の写真。
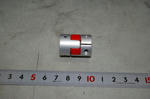
何だと思います?
モーターとギヤボックスを繋ぐカップリング。
どんなに頑張っても、モーターシャフトとギヤボックスシャフトの中心線の誤差ゼロは不可能です。
もし、直接接続し、ホンの少しでも誤差が有ったら、軸受けに掛かる負担はかなりの物。
其処を和らげるのがフレキシブルジョイント。
一般にはゴム製等が使われていますが、僕の使用にはブッブー。
兎に角、モーターの駆動をロス無くターンテーブルに伝えたいのです。
チョットでもモーターの正確な回転をターンテーブルに伝えない構造は取りたく有りません。
つまり、ある程度の自由があり、回転方向の遊びはゼロに近い物。
結構、ジョイントは製品化されていますが、この辺はカタログでは判らない。
モーターと同じメーカーのジョイントを買ってみました。
此れがバッチリ。フレキシブルなんて言葉、使っちゃ拙いんじゃないの。ってくらいガタが無い。
モーターの位置出しには苦労しそうですが、使えそう。
ちなみにシャフトの中心誤差の許容範囲。
並行に0.15mm以内、角度は1°以内。
出来たら、その範囲の1/3以下での使用を推薦。と成っている。
僕の腕を試されそう。
失敗は出来なくなった。有言実行は辛い。
で、下の写真。
何だと思います?
モーターとギヤボックスを繋ぐカップリング。
どんなに頑張っても、モーターシャフトとギヤボックスシャフトの中心線の誤差ゼロは不可能です。
もし、直接接続し、ホンの少しでも誤差が有ったら、軸受けに掛かる負担はかなりの物。
其処を和らげるのがフレキシブルジョイント。
一般にはゴム製等が使われていますが、僕の使用にはブッブー。
兎に角、モーターの駆動をロス無くターンテーブルに伝えたいのです。
チョットでもモーターの正確な回転をターンテーブルに伝えない構造は取りたく有りません。
つまり、ある程度の自由があり、回転方向の遊びはゼロに近い物。
結構、ジョイントは製品化されていますが、この辺はカタログでは判らない。
モーターと同じメーカーのジョイントを買ってみました。
此れがバッチリ。フレキシブルなんて言葉、使っちゃ拙いんじゃないの。ってくらいガタが無い。
モーターの位置出しには苦労しそうですが、使えそう。
ちなみにシャフトの中心誤差の許容範囲。
並行に0.15mm以内、角度は1°以内。
出来たら、その範囲の1/3以下での使用を推薦。と成っている。
僕の腕を試されそう。
今掛かっている、アンプの製作は、シャシのアルマイト加工で小休止。
頭の中は、ギヤボックスの事でいっぱい。
モーターを廻しながら、ギヤボックスの作図です。
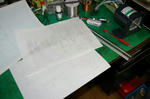
作図中も右で回っているモーター。静かで回っているのを忘れそう。
何しろ、初めて作るギヤボックス。
メタルはどうするか。シャフトの材質は何が良いか。オイル潤滑はどうするか。オイルが漏れないようにシーリングはどうするか。
考えなくてはいけない事が山積みです。
メタルも自分で作るか、出来合いを利用するか?
こんな時、下手な考え休むに似たり。
兎に角手を動かして試作するのが一番の近道。
アルマイトが上がってくるのは水曜日。
其れ迄に手配できるパーツのリストを作り、明日発注。
旋盤のバイトの刃も、手持ちの物では間に合わなくなりそう。
ロングドリル(勿論精密刃)も何本か買う様。
新製品を作る度に、加工の刃が増えてます。
で、実はチョットカッコいいデザインを考えています(勿論、実用性にもプラスのデザイン)。
今はナ・イ・ショ。
頭の中は、ギヤボックスの事でいっぱい。
モーターを廻しながら、ギヤボックスの作図です。
作図中も右で回っているモーター。静かで回っているのを忘れそう。
何しろ、初めて作るギヤボックス。
メタルはどうするか。シャフトの材質は何が良いか。オイル潤滑はどうするか。オイルが漏れないようにシーリングはどうするか。
考えなくてはいけない事が山積みです。
メタルも自分で作るか、出来合いを利用するか?
こんな時、下手な考え休むに似たり。
兎に角手を動かして試作するのが一番の近道。
アルマイトが上がってくるのは水曜日。
其れ迄に手配できるパーツのリストを作り、明日発注。
旋盤のバイトの刃も、手持ちの物では間に合わなくなりそう。
ロングドリル(勿論精密刃)も何本か買う様。
新製品を作る度に、加工の刃が増えてます。
で、実はチョットカッコいいデザインを考えています(勿論、実用性にもプラスのデザイン)。
今はナ・イ・ショ。