QRKの修理が終わりました。
千切れなかった1個のゴムクッション。
1mm厚位のゴムでぶら下げる形で使っています。
その様な使い方ですから、どうしても伸びて来てしまうんですね。
僕が作っているクッション。
ソルボセインを圧縮方向に使っています。
もう10年以上前から作っていますが、未だにゴムを交換した人はいません。
アルミ削りだしのブラケットでソルボセインを挟んでいます。
万が一ソルボセインが痛んでも、その部分だけの交換で済みますので、長期に渡っての使用が可能です。
で、QRKを使う時の一番大切な事。
アイドラーの圧着調整です。
HPの方に詳しく書いて有ります。
一度調整すると其の侭使用可能・・・・・・・・・。
じゃ無いんですね。頻繁な調整を必要とします。
調整ネジにロック機構が無いので、自然と緩んでくるのです。
拙い事に緩む方向はアイドラーをドンドン圧着させる方向。
其の侭使うと壊れます。
電源SWを入れ、シフトノブを動かす時に、ノブが吸い込まれるように入ったら、間違いなく圧着し過ぎ。
この状態で使っている方が非常に多いんですね。
ハイ、脅かしではなく壊れます。
で、僕が作ったアイドラードライブのターンテーブルは調整ネジにロック機構をつけました。
プロ機って判っている人が使うのを条件で作られているのが多いんですね。
頻繁なメンテも必要とします。
プロ機と民生機の違い。
何にも手を掛けずに使うなら民生機の方が長持ちします。
でも定期的なメンテをしたら、プロ機は民生機の何倍も長持ちします。
プロ機に手を出すのはこの辺が判っていないと難しいですね。
千切れなかった1個のゴムクッション。
1mm厚位のゴムでぶら下げる形で使っています。
その様な使い方ですから、どうしても伸びて来てしまうんですね。
僕が作っているクッション。
ソルボセインを圧縮方向に使っています。
もう10年以上前から作っていますが、未だにゴムを交換した人はいません。
アルミ削りだしのブラケットでソルボセインを挟んでいます。
万が一ソルボセインが痛んでも、その部分だけの交換で済みますので、長期に渡っての使用が可能です。
で、QRKを使う時の一番大切な事。
アイドラーの圧着調整です。
HPの方に詳しく書いて有ります。
一度調整すると其の侭使用可能・・・・・・・・・。
じゃ無いんですね。頻繁な調整を必要とします。
調整ネジにロック機構が無いので、自然と緩んでくるのです。
拙い事に緩む方向はアイドラーをドンドン圧着させる方向。
其の侭使うと壊れます。
電源SWを入れ、シフトノブを動かす時に、ノブが吸い込まれるように入ったら、間違いなく圧着し過ぎ。
この状態で使っている方が非常に多いんですね。
ハイ、脅かしではなく壊れます。
で、僕が作ったアイドラードライブのターンテーブルは調整ネジにロック機構をつけました。
プロ機って判っている人が使うのを条件で作られているのが多いんですね。
頻繁なメンテも必要とします。
プロ機と民生機の違い。
何にも手を掛けずに使うなら民生機の方が長持ちします。
でも定期的なメンテをしたら、プロ機は民生機の何倍も長持ちします。
プロ機に手を出すのはこの辺が判っていないと難しいですね。
暫らく振りにQRKの修理です。そう、整備ではなく修理。
QRKはモーターの振動を伝えない為に、モーターボードを3個のゴムクッションでフローティングしています。
このゴムが持たないんですね。
見事に2箇所がちぎれて・・・・・・・・・・。
此処のゴム。理想的には3年で交換。持たせても5年。
もう純正のクッションは入手できませんので、此処の部分の対策品を僕の所で作っています。
この個体、もっと早く持って来てくれていれば・・・・・・・・。
クッションがへたった状態で使うと、アイドラーが段付き磨耗をしてしまうんですね。
この場合、アイドラーの交換しか有りません。
製造が中止されてから20年以上経っていますし、輸入元も閉鎖されました。
製造中止の時点で、パーツのストックを図った(僕の店の器ですから、大量購入は資金の点で無理)のですが、流石に底をつきました。
アイドラーを作ってくれる所も無くなりました。
最後の手持ちのアイドラーを使って修理します。
今後のアイドラー交換は出来ません。
まだ、ゴムクッションを対策品に換えていない方は、至急の交換をお勧めします。
アイドラーが段付き磨耗しますと、修理不能に成りますので・・。
機械(アンプも含む)を長持ちさせたいのなら、壊れてからの修理では遅いんですね。
壊れる前のメンテナンスが長持ちさせる唯一の方法です。
只、僕の方からは声掛けいたしません。
商売って思われるのがイヤなんです。
お得意様のメンテ状態はカルテが有るので判っています。
気になったら、声を掛けてください。
必要か、まだ大丈夫かその場で返事が出来ますので。
追記です。
アンプの場合、製造後20年経ったら真空管ソケットは全交換をお勧めします。
昨日完成したターンテーブル軸受けとターンテーブルシャフト。
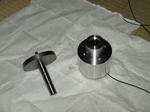
シャフトは80mm径の45c丸棒からの削り出し。
軸受けも同じく80Φのアルミ丸棒に砲金スリーブを焼き嵌め。
スラスト受け(ターンテーブルの全加重を受けます)は僕自慢のダブルボール受け。
糸ドライブは駆動力がベルトやアイドラーよりも弱くなり勝ち(駆動力の接触面積が小さい)。
結果、チョットのフリクションムラが回転ムラを起こします。
軸受けの接触面積を減らせば解決するのですが、耐久性の点で問題です。
その辺の絡みを解決したのがダブルボール受けなんですね。
問題は機械精度。量産品では無理な構造かも知れません。
この方式。万が一磨耗しても鋼球の交換だけで済みますから、殆ど半永久的に使えます。
要求するのは数年に一度のオイル交換。
使用するオイルは一般市販のエンジンオイルでOKと言う・・・・・・・(笑)。
僕が入れているのはモチュールの300V+EPL(バイクと勘違いしています、汗)。
僕の軸受け、使い出して丸6年。
先日開けて見ましたが、磨耗は見られず、馴染みも未だ済んでいない様子です。
馴染むのにも10年位は掛かりそうですね。
注意です。使用オイル、一般市販のエンジンオイル以外は絶対に使わないで下さい。特にオーディオ雑誌等で薦める植物油や動物油は厳禁です。
以前QRKで使った方がいまして、とんでもない修理費が掛かりました。
基本的に鉱物油か化学合成油(勿論潤滑用)です。
シャフトは80mm径の45c丸棒からの削り出し。
軸受けも同じく80Φのアルミ丸棒に砲金スリーブを焼き嵌め。
スラスト受け(ターンテーブルの全加重を受けます)は僕自慢のダブルボール受け。
糸ドライブは駆動力がベルトやアイドラーよりも弱くなり勝ち(駆動力の接触面積が小さい)。
結果、チョットのフリクションムラが回転ムラを起こします。
軸受けの接触面積を減らせば解決するのですが、耐久性の点で問題です。
その辺の絡みを解決したのがダブルボール受けなんですね。
問題は機械精度。量産品では無理な構造かも知れません。
この方式。万が一磨耗しても鋼球の交換だけで済みますから、殆ど半永久的に使えます。
要求するのは数年に一度のオイル交換。
使用するオイルは一般市販のエンジンオイルでOKと言う・・・・・・・(笑)。
僕が入れているのはモチュールの300V+EPL(バイクと勘違いしています、汗)。
僕の軸受け、使い出して丸6年。
先日開けて見ましたが、磨耗は見られず、馴染みも未だ済んでいない様子です。
馴染むのにも10年位は掛かりそうですね。
注意です。使用オイル、一般市販のエンジンオイル以外は絶対に使わないで下さい。特にオーディオ雑誌等で薦める植物油や動物油は厳禁です。
以前QRKで使った方がいまして、とんでもない修理費が掛かりました。
基本的に鉱物油か化学合成油(勿論潤滑用)です。
昨日の夕方、ガラードの軸受けを組み上げました。
と言っても、底部は液体パッキンでシールしましたので、パッキンが乾燥してからで無いと、漏れチェックは出来ません。
と言う事で一晩放置。
今日は朝から出かける用事。結局24時間放置してました。
今帰って来て、直ぐに軸受けのチェック。
漏れてないよねー・・(ハラハラ)。
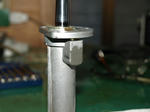
メタルパテで埋めた横部分。
丸っ切りオイル気ゼロ。手で触ってもオイルの感触なし。
成功ですね。
で、一番問題の底部(此れの修理が本題)。
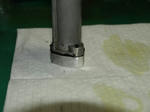
写真で判りますよね。下に敷いたウエスにシミが全然有りません。
此処もオイル漏れゼロ。
で、新しく作った底部と本体の間に見える黒いもの。
はみ出した液体パッキンです。
勿論、完全硬化済みですので、手で触れても大丈夫。
さて、明日は組み上げ。
受けた他の部分も完成してますので、近々納品です。
と言っても、底部は液体パッキンでシールしましたので、パッキンが乾燥してからで無いと、漏れチェックは出来ません。
と言う事で一晩放置。
今日は朝から出かける用事。結局24時間放置してました。
今帰って来て、直ぐに軸受けのチェック。
漏れてないよねー・・(ハラハラ)。
メタルパテで埋めた横部分。
丸っ切りオイル気ゼロ。手で触ってもオイルの感触なし。
成功ですね。
で、一番問題の底部(此れの修理が本題)。
写真で判りますよね。下に敷いたウエスにシミが全然有りません。
此処もオイル漏れゼロ。
で、新しく作った底部と本体の間に見える黒いもの。
はみ出した液体パッキンです。
勿論、完全硬化済みですので、手で触れても大丈夫。
さて、明日は組み上げ。
受けた他の部分も完成してますので、近々納品です。
チョイ中断していますガラードの修理。
イエ、サボっているんじゃないですよ。メタルパテの硬化待ち。
この辺の素材は化学反応で硬化します。この硬化時間、周辺温度で偉く違うんですね。
要は、低温ほど時間が掛かる。
引っ越した場所。もう氷が張ってます・・・・・(汗)。
こんな所に引っ越したので、時間をしっかりと見ないで次の作業に入ったら・・(大汗)。
昔、小学生時代、僕はプラモ小僧でした。接着剤の硬化が待てなくて次の作業へ・・・。
ハイ、痛い目にいっぱい会って学習しました。急いては事を仕損じるって・・。
慌てる乞食はもらいが少ないとも言いますね。
物作りは、急いで良い事はまず有りません。急ぐ人・・・もう少し人生の勉強を(笑)。
で、二日間置きました。流石に硬化は終った筈。
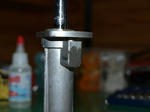
この写真を見て、『なんだパテで塞いだだけじゃないか。』って思ったらブッブー。
内情は・・・・・・・・・。
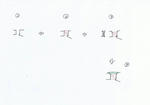
メタルパテで穴を塞ぐ。そりゃ塞ぐだけなら簡単。
でもね、今回の穴、奥に通路が有るんですね。通路を塞がないでメタルパテを充填。
出来ます・・・・・?
まあ、やって出来ない事は無いと思いますけど、自分の物ならいざ知らず、人の物です。ギャンブルは出来ません。
で、上図の様にしたんですね。
正しく言うと、メタルパテは使わないでも行けると踏んだんです。
で、図の赤い部分。真鍮でピンを作り圧入。簡単に書いちゃいますが、ピンの径は・・・?
穴の内径を計るのは非常に難しいんです。そりゃプラマイ0,数ミリの誤差が許されるんでしたら何でもOK。
今回の場合、内径に対してプラス3/100mmのピンを作るんですね。
しかも穴の内径は不明。
まず、元々入っていたピン径を測ります。4,91mmでした。
で、ピンを動かして手探りでピンと穴との隙間を・・・・・(笑)。
人間の手って素晴らしく、1/100mmが判ります。今回の感触では隙間は3/100mm(笑)。
と言う事は穴径は4,94mm。
此れに対して、3/100mm太いピンを作ります。つまり4,97mmのピンです。
アルミの本体にスムーズに圧入する事の出来る材質。
今回は真鍮をチョイス。
②の様にしたんですね。
この状態で組みました。正常ならオイル漏れは無い筈。
無論、圧入の感触は良い感じ。緩くも無くきつ過ぎも無く。
組み上げて小一時間でオイルの滲みが見られたんです。
拙いよなー。此処までやっても滲むのか・・・・。
微妙に穴が真円ではないのかも・・?
と言う事で、次の作戦。
③の形にフライスで切削。この時大事なのはオイルを一切使わない。切削油厳禁。
切削後、兎に角しつこくパーツクリーナーで脱脂。
数時間様子見。微細な隙間からオイルが滲んで来ないかを見ます。
大丈夫って確認が出来たなら、此処で最終作業、メタルパテを凹んだ所に塗りこみます。
メタルパテ、オーディオの世界ではあまり知られていませんね。
趣味のバイクの世界では極普通に使用。
パテですが、硬化すると金属並みの強度を持ち、オイルに犯されませんし、ネジを切ってもOKと言う優れものです。
エポキシは長時間オイルに晒されますと、接着が剥がれてしまう恐れが大きいんです(まず駄目です)。
メタルパテはクランクケースの破損(小さな部分)の補修にも使われる凄い素材なんですね。
今日の夕方に軸受けを組み上げ、オイル漏れのチェック中が最初の写真です。
もう6時間以上経っていますが滲みゼロ。
ヤットオイル漏れが治ったようですね。
まあ、バイクの世界でもオイル漏れをゼロにするって結構大変(略不可能)な事なんですけど・・。
イエ、サボっているんじゃないですよ。メタルパテの硬化待ち。
この辺の素材は化学反応で硬化します。この硬化時間、周辺温度で偉く違うんですね。
要は、低温ほど時間が掛かる。
引っ越した場所。もう氷が張ってます・・・・・(汗)。
こんな所に引っ越したので、時間をしっかりと見ないで次の作業に入ったら・・(大汗)。
昔、小学生時代、僕はプラモ小僧でした。接着剤の硬化が待てなくて次の作業へ・・・。
ハイ、痛い目にいっぱい会って学習しました。急いては事を仕損じるって・・。
慌てる乞食はもらいが少ないとも言いますね。
物作りは、急いで良い事はまず有りません。急ぐ人・・・もう少し人生の勉強を(笑)。
で、二日間置きました。流石に硬化は終った筈。
この写真を見て、『なんだパテで塞いだだけじゃないか。』って思ったらブッブー。
内情は・・・・・・・・・。
メタルパテで穴を塞ぐ。そりゃ塞ぐだけなら簡単。
でもね、今回の穴、奥に通路が有るんですね。通路を塞がないでメタルパテを充填。
出来ます・・・・・?
まあ、やって出来ない事は無いと思いますけど、自分の物ならいざ知らず、人の物です。ギャンブルは出来ません。
で、上図の様にしたんですね。
正しく言うと、メタルパテは使わないでも行けると踏んだんです。
で、図の赤い部分。真鍮でピンを作り圧入。簡単に書いちゃいますが、ピンの径は・・・?
穴の内径を計るのは非常に難しいんです。そりゃプラマイ0,数ミリの誤差が許されるんでしたら何でもOK。
今回の場合、内径に対してプラス3/100mmのピンを作るんですね。
しかも穴の内径は不明。
まず、元々入っていたピン径を測ります。4,91mmでした。
で、ピンを動かして手探りでピンと穴との隙間を・・・・・(笑)。
人間の手って素晴らしく、1/100mmが判ります。今回の感触では隙間は3/100mm(笑)。
と言う事は穴径は4,94mm。
此れに対して、3/100mm太いピンを作ります。つまり4,97mmのピンです。
アルミの本体にスムーズに圧入する事の出来る材質。
今回は真鍮をチョイス。
②の様にしたんですね。
この状態で組みました。正常ならオイル漏れは無い筈。
無論、圧入の感触は良い感じ。緩くも無くきつ過ぎも無く。
組み上げて小一時間でオイルの滲みが見られたんです。
拙いよなー。此処までやっても滲むのか・・・・。
微妙に穴が真円ではないのかも・・?
と言う事で、次の作戦。
③の形にフライスで切削。この時大事なのはオイルを一切使わない。切削油厳禁。
切削後、兎に角しつこくパーツクリーナーで脱脂。
数時間様子見。微細な隙間からオイルが滲んで来ないかを見ます。
大丈夫って確認が出来たなら、此処で最終作業、メタルパテを凹んだ所に塗りこみます。
メタルパテ、オーディオの世界ではあまり知られていませんね。
趣味のバイクの世界では極普通に使用。
パテですが、硬化すると金属並みの強度を持ち、オイルに犯されませんし、ネジを切ってもOKと言う優れものです。
エポキシは長時間オイルに晒されますと、接着が剥がれてしまう恐れが大きいんです(まず駄目です)。
メタルパテはクランクケースの破損(小さな部分)の補修にも使われる凄い素材なんですね。
今日の夕方に軸受けを組み上げ、オイル漏れのチェック中が最初の写真です。
もう6時間以上経っていますが滲みゼロ。
ヤットオイル漏れが治ったようですね。
まあ、バイクの世界でもオイル漏れをゼロにするって結構大変(略不可能)な事なんですけど・・。
昨日、横からのオイル漏れが発見された軸受け。
あの時点では、ピンの周りの肉を若干削り、其の部分をサンドブラスト(此れで完璧に脱脂出来ます)。
其処の凹みにメタルパテを塗りこむ予定でした。
でも其れが最良との判断が付かなくて、あーだこーだ頭の中で考えていたんですね。
寝付くまで、布団の中でまで考えている始末。
で、今朝もう一度軸受けを見たら・・・・・・。
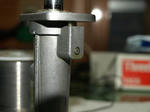
昨日綺麗に拭き取った所から、またもやのオイル漏れです。こりゃ、結構重症かな?
圧力が掛かっている訳でもなく、自然に此れだけ滲み出すと言うのは・・・・・。
下手な考え休むに似たり。
兎に角ピン周りを削ってみよう。
ピン穴の内径は5mm弱。
5mmのドリルをフライスにセット。中心点をジックリ捉えて、ジワッとドリルの刃を当てます。
中心点が少しずつ掘れて来て、本体のアルミ部に刃が当たった瞬間・・・・・・。
ピンが空回りして抜けて来た。
ヘッ・・・・・・・。
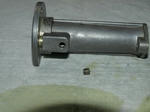
あっ気なく抜けたピン。
差し込むとユルユル。
穴の中を見て下さい。内側の奥に出っ張りが有り、これ以上ピンが入らない様に成っています。
で、打ち込まれていたピンの頭。中心に小さな凹みが有りました。
つまり、緩いピンを差し込んで、頭の中心をポンチの様な物で打撃。
するとピンの頭が広がって、穴をふさぐ。
と、こんな感じでのピンの固定だったようです(リベットの止め方に似てますね)。
結果、頭の広がった部分をホンのチョイ削ったら、簡単に抜け出して・・・・・。
此れで、修理の方法は決定。
どうするかは続編で(笑)。
あの時点では、ピンの周りの肉を若干削り、其の部分をサンドブラスト(此れで完璧に脱脂出来ます)。
其処の凹みにメタルパテを塗りこむ予定でした。
でも其れが最良との判断が付かなくて、あーだこーだ頭の中で考えていたんですね。
寝付くまで、布団の中でまで考えている始末。
で、今朝もう一度軸受けを見たら・・・・・・。
昨日綺麗に拭き取った所から、またもやのオイル漏れです。こりゃ、結構重症かな?
圧力が掛かっている訳でもなく、自然に此れだけ滲み出すと言うのは・・・・・。
下手な考え休むに似たり。
兎に角ピン周りを削ってみよう。
ピン穴の内径は5mm弱。
5mmのドリルをフライスにセット。中心点をジックリ捉えて、ジワッとドリルの刃を当てます。
中心点が少しずつ掘れて来て、本体のアルミ部に刃が当たった瞬間・・・・・・。
ピンが空回りして抜けて来た。
ヘッ・・・・・・・。
あっ気なく抜けたピン。
差し込むとユルユル。
穴の中を見て下さい。内側の奥に出っ張りが有り、これ以上ピンが入らない様に成っています。
で、打ち込まれていたピンの頭。中心に小さな凹みが有りました。
つまり、緩いピンを差し込んで、頭の中心をポンチの様な物で打撃。
するとピンの頭が広がって、穴をふさぐ。
と、こんな感じでのピンの固定だったようです(リベットの止め方に似てますね)。
結果、頭の広がった部分をホンのチョイ削ったら、簡単に抜け出して・・・・・。
此れで、修理の方法は決定。
どうするかは続編で(笑)。
今日は朝からフライス仕事。もちバイクではなく仕事ですよー(笑)。
一日中立ち仕事。チョイ疲れた。
で、工場から離れ、母屋の作業机の上。
1日前から、ガラードの軸受けを逆さから正常の向きにして、オイルの漏れの確認を・・。
大きな事を言って作った軸受けベースからオイルが漏れたら笑い者。
単に作っただけでの納品は怖いんですね。
机の上で直立している軸受け。
見たら・・・・・・・・・。
オイルにまみれている。オイオイ・・・・・・・。
僕の作った底板からのオイル漏れなら、下部しか濡れていない筈。
ところがかなり上から濡れているんですね。
ハ~~~~~?
オイルを拭き取ってからイケネ。ブログのネタを消しちゃった(汗)。
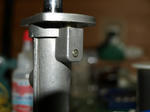
拭き取った後の写真ですので綺麗です。
写真の丸い部分。
昨日アップした図面を見て下さい。
オイル注入口。真上から垂直に開いた穴、途中で水平に・・・・。
穴を開ける時、途中で直角に曲げるのは今の技術でも不可能(笑)。
で、この様な場合、垂直と水平の両方に穴を開け、要らない部分に蓋をして済ませるんですね。
写真の丸いピンの様な物が、其のメクラ蓋なのです。
横穴の不必要な部分に、ピンを圧入して穴を塞ぐのです。
で、此処から漏れている・・・・・・・・。
前の図面から判るでしょうが、此処から漏れると上部のメタルにはオイルが行かなくなってしまうんですね。
今回バラして、上部のメタル部分にオイル気がまったく無かった理由が判りました。
底からの漏れと、メクラピンからのダブルお漏らしだったのです。
発見して、さてどう治そう。
単純にエポキシなんかを塗ったらブッブー。
ピンと本体の間にオイルが入っていますから、エポキシが固まる前にオイルが滲み出してくるんですね。
接着面にはオイル厳禁。
更に、煩く言うと(とっても大事)、金属って結晶の集まりなんですね。其の結晶の隙間にもオイルが入っているんです。
表面の脱脂(パーツクリーナーの吹きつけ)程度ではオイル気を無くすのは無理。
完全な脱脂をしないと、近い将来に再び漏れ出します。
面倒だけど、あの方法しかないかな・・?
今日は時間切れ。明日頑張ります(天気が悪いと出来ないんですが)。
一日中立ち仕事。チョイ疲れた。
で、工場から離れ、母屋の作業机の上。
1日前から、ガラードの軸受けを逆さから正常の向きにして、オイルの漏れの確認を・・。
大きな事を言って作った軸受けベースからオイルが漏れたら笑い者。
単に作っただけでの納品は怖いんですね。
机の上で直立している軸受け。
見たら・・・・・・・・・。
オイルにまみれている。オイオイ・・・・・・・。
僕の作った底板からのオイル漏れなら、下部しか濡れていない筈。
ところがかなり上から濡れているんですね。
ハ~~~~~?
オイルを拭き取ってからイケネ。ブログのネタを消しちゃった(汗)。
拭き取った後の写真ですので綺麗です。
写真の丸い部分。
昨日アップした図面を見て下さい。
オイル注入口。真上から垂直に開いた穴、途中で水平に・・・・。
穴を開ける時、途中で直角に曲げるのは今の技術でも不可能(笑)。
で、この様な場合、垂直と水平の両方に穴を開け、要らない部分に蓋をして済ませるんですね。
写真の丸いピンの様な物が、其のメクラ蓋なのです。
横穴の不必要な部分に、ピンを圧入して穴を塞ぐのです。
で、此処から漏れている・・・・・・・・。
前の図面から判るでしょうが、此処から漏れると上部のメタルにはオイルが行かなくなってしまうんですね。
今回バラして、上部のメタル部分にオイル気がまったく無かった理由が判りました。
底からの漏れと、メクラピンからのダブルお漏らしだったのです。
発見して、さてどう治そう。
単純にエポキシなんかを塗ったらブッブー。
ピンと本体の間にオイルが入っていますから、エポキシが固まる前にオイルが滲み出してくるんですね。
接着面にはオイル厳禁。
更に、煩く言うと(とっても大事)、金属って結晶の集まりなんですね。其の結晶の隙間にもオイルが入っているんです。
表面の脱脂(パーツクリーナーの吹きつけ)程度ではオイル気を無くすのは無理。
完全な脱脂をしないと、近い将来に再び漏れ出します。
面倒だけど、あの方法しかないかな・・?
今日は時間切れ。明日頑張ります(天気が悪いと出来ないんですが)。
暫らくぶりにガラードの整備が入ってきました。整備と言っても僕の所にはガラードのパーツは有りません。
要は、僕のHPに書いて有る事の再現です。
HPに『ガラードの軸受けはオイルが漏れて入っていません。』なんて書いちゃったもんですから・・(笑)。
基本的に軸受けにはオイルが必要。其れが抜けてなくなってしまうと言うのですから、気に成って当然な事なんです(無関心の人が多過ぎますね)。
で、その辺をHPよりも更に詳しく書いてしまおう。なんて魂胆です。

ご存知、ガラード301の軸受けです。401も同じと思うのですが整備に持ち込まれるのは301だけでしたので401は判りません。
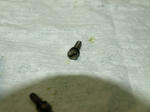
ガラードの止めネジはマイナスが主流。と言うかプラスネジは有ったかな?
インチネジですので駄目にしちゃうと大変です。簡単に入手出来ないんですから。
で・・・・・・・。
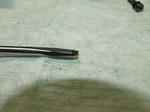
愛用のドライバー。ご存知PB。
歯先がテーパーに成っていないので、ネジへのダメージが少ないのです。
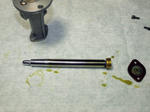
分解して直ぐの写真。
ペーパーウェスの上でバラしてもオイルのシミが少ないですね。
つまり、殆どオイルが入っていなかった。
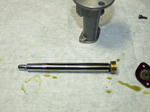
上の写真から数分後。
違いが判りますか?
軸受けの位置が変わっていますよね。
数分放置したならば、軸受けの置いてあった位置には、大量のオイルのシミが出来る筈。
丸っ切り有りません。
つまり軸受けの中にオイルが殆ど入っていなかったのです。
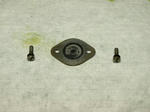
其の犯人。
軸受けの底蓋。
たった2mmの厚みしか有りません。しかも2本のネジで止まっているだけ。
この蓋の中心部に回転系の全ての重量が掛かります。
この形ですから、真ん中が重量に負けてたわみます。
そう成ると、軸受け本体との間に隙間が出来て・・・・・・・・。
此れがオイルの漏れる原因です。
過去に結構な数の軸受けをばらしましたが、オイルの入っていた個体はゼロ。
間違いなく、設計ミスです。
で、軸受けの上にオイル注入口が有るので、皆さん其処から足していると思うのですが・・・・・。
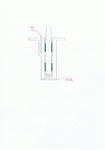
絵の下手さはご勘弁を。
此れが軸受けの断面図です。
確かにオイル注入口は有るのですが、オイルの抜けた軸受けの中には空気が入ってます。注入口からオイルを入れても、空気の逃げる通路が確保されていません。
つまり、中の空気が邪魔をして、オイルは入り口でストップ。
すると、普通の人は入り口に溢れたので内部はオイルでいっぱいと考えちゃう(僕だってそう考えます)。
オイル注入口も役に立たないんですね。
で、僕のオイルの入れ方。
写真は有りません。両手がオイルまみれでカメラを操作できないんですね。
まず底蓋を外します。
軸受けを真っ直ぐに立てて持ちます(シャフトを下に落とさないように)。
シャフトを下にずらします。抜いちゃ駄目ですよ。
シャフトのテーパー部が上のスリーブの下端よりも若干下の位置まで。
そうすると、空気の逃げ口が出来るんですね。
其の状態を片手で維持。
もう一方の手で、オイル注入口にオイル注しでオイルを圧送します。
シャフトと軸受けの間からオイルが出るまで続けます。
上下のスリーブ間のオイル溜めの容量が結構有りますので、結構な量が入ります。
シャフトとスリーブの隙間は狭いので、下にオイルは出て来ません(シャフト、スリーブに異常が有ると漏れます)。
オイルが充分入ったら、下からシャフトを押し上げます。オイルがこぼれますがしかたが有りません。
その位置で、オイル注入口に蓋をします。
そのまま逆さに。
底のへこんだ部分に少量のオイルを入れます。スラスト受けが入りますので、其の分を調整して・・。
オイルを入れたら、スラスト受けを挿入。
オイルが若干溢れるくらいが適量。
溢れたオイルを拭き取り、更に底板と接する面を脱脂。
間に入るパッキンも脱脂。
パッキンの当たる、軸受け側と底板側に少量の液体パッキンを塗布。
この状態で底板の取り付け(勿論間にはパッキンを)。
液体パッキンの完全乾燥まで絶対に動かさない(さかさまの状態)。
なんてやっても、ノーマルの底板ではまた直ぐに漏れるので・・・・・・。
軽く追記です。
今回ガラードが俎上に上がりましたが、イギリス製の工業製品には非常に多い事なんです。
ヤハリ国民性なのですか。
電気的には賢いなーと言う設計が見られるのですが、機械的には・・・・・・?
スピーカーユニットしかり、バイク(笑)しかり・・、あ車もか。
要は、僕のHPに書いて有る事の再現です。
HPに『ガラードの軸受けはオイルが漏れて入っていません。』なんて書いちゃったもんですから・・(笑)。
基本的に軸受けにはオイルが必要。其れが抜けてなくなってしまうと言うのですから、気に成って当然な事なんです(無関心の人が多過ぎますね)。
で、その辺をHPよりも更に詳しく書いてしまおう。なんて魂胆です。
ご存知、ガラード301の軸受けです。401も同じと思うのですが整備に持ち込まれるのは301だけでしたので401は判りません。
ガラードの止めネジはマイナスが主流。と言うかプラスネジは有ったかな?
インチネジですので駄目にしちゃうと大変です。簡単に入手出来ないんですから。
で・・・・・・・。
愛用のドライバー。ご存知PB。
歯先がテーパーに成っていないので、ネジへのダメージが少ないのです。
分解して直ぐの写真。
ペーパーウェスの上でバラしてもオイルのシミが少ないですね。
つまり、殆どオイルが入っていなかった。
上の写真から数分後。
違いが判りますか?
軸受けの位置が変わっていますよね。
数分放置したならば、軸受けの置いてあった位置には、大量のオイルのシミが出来る筈。
丸っ切り有りません。
つまり軸受けの中にオイルが殆ど入っていなかったのです。
其の犯人。
軸受けの底蓋。
たった2mmの厚みしか有りません。しかも2本のネジで止まっているだけ。
この蓋の中心部に回転系の全ての重量が掛かります。
この形ですから、真ん中が重量に負けてたわみます。
そう成ると、軸受け本体との間に隙間が出来て・・・・・・・・。
此れがオイルの漏れる原因です。
過去に結構な数の軸受けをばらしましたが、オイルの入っていた個体はゼロ。
間違いなく、設計ミスです。
で、軸受けの上にオイル注入口が有るので、皆さん其処から足していると思うのですが・・・・・。
絵の下手さはご勘弁を。
此れが軸受けの断面図です。
確かにオイル注入口は有るのですが、オイルの抜けた軸受けの中には空気が入ってます。注入口からオイルを入れても、空気の逃げる通路が確保されていません。
つまり、中の空気が邪魔をして、オイルは入り口でストップ。
すると、普通の人は入り口に溢れたので内部はオイルでいっぱいと考えちゃう(僕だってそう考えます)。
オイル注入口も役に立たないんですね。
で、僕のオイルの入れ方。
写真は有りません。両手がオイルまみれでカメラを操作できないんですね。
まず底蓋を外します。
軸受けを真っ直ぐに立てて持ちます(シャフトを下に落とさないように)。
シャフトを下にずらします。抜いちゃ駄目ですよ。
シャフトのテーパー部が上のスリーブの下端よりも若干下の位置まで。
そうすると、空気の逃げ口が出来るんですね。
其の状態を片手で維持。
もう一方の手で、オイル注入口にオイル注しでオイルを圧送します。
シャフトと軸受けの間からオイルが出るまで続けます。
上下のスリーブ間のオイル溜めの容量が結構有りますので、結構な量が入ります。
シャフトとスリーブの隙間は狭いので、下にオイルは出て来ません(シャフト、スリーブに異常が有ると漏れます)。
オイルが充分入ったら、下からシャフトを押し上げます。オイルがこぼれますがしかたが有りません。
その位置で、オイル注入口に蓋をします。
そのまま逆さに。
底のへこんだ部分に少量のオイルを入れます。スラスト受けが入りますので、其の分を調整して・・。
オイルを入れたら、スラスト受けを挿入。
オイルが若干溢れるくらいが適量。
溢れたオイルを拭き取り、更に底板と接する面を脱脂。
間に入るパッキンも脱脂。
パッキンの当たる、軸受け側と底板側に少量の液体パッキンを塗布。
この状態で底板の取り付け(勿論間にはパッキンを)。
液体パッキンの完全乾燥まで絶対に動かさない(さかさまの状態)。
なんてやっても、ノーマルの底板ではまた直ぐに漏れるので・・・・・・。
軽く追記です。
今回ガラードが俎上に上がりましたが、イギリス製の工業製品には非常に多い事なんです。
ヤハリ国民性なのですか。
電気的には賢いなーと言う設計が見られるのですが、機械的には・・・・・・?
スピーカーユニットしかり、バイク(笑)しかり・・、あ車もか。