プーリーと糸が微弱ながらスリップを起こしている。
その問題を解決するには、プーリーの回転数を落とせば良い。
ハイ、いたって簡単です。モーターの回転数を減速するだけですから・・。
で、その減速機構。騒音は一切ご法度。此れが難しい。コクドベルトやギヤ、どちらも騒音が付きまとう。
糸で二段減速。
此れも散々考えたんだけど、糸のテンションの取り方が難しい。プーリーの精度も大変。
自分だけが使う前提で、コスト(工数)を無視すりゃ出来ない事は無いけど、お客様に出す時の価格は抑えたい。
しかも、使い方が非常にクリティカルでは、一般の音楽ファンには使いこなせない。
そうなんです。自分だけが使うのならどんな方法も有るんですが、市販をする。もの凄く縛られるのです。
何とか減速をしたい。ウジウジの数年間だったのです。
そんな折、あるお客様が・・・・・・。
『カッティングマシンを買った。ピンキーさんの糸ドライブよりも良い。』
こんな電話を頂いたんですね。
まあ、普通の人間なら、カッティングマシンには敵う筈も無いよなー。
って考えるんでしょうが、普通の人間ではないピンキー君。
『プツン。』
切れちゃった。永年のウジウジが溜まりに溜まっていたんですね。
早速、そのカッティングマシンを見せてもらう。
かなりの年代物。駆動方式はギヤドライブ。ギヤにはウォームを使っている。
で、そのギヤボックスとターンテーブルの結合に、ギヤの騒音とシャフトの位置のずれの逃げの為にゴムを使っている。
そうか、確かにウォームなら騒音は少ない。
ターンテーブルとのゴム結合が有るのなら、こちらにも勝算が・・・・・。
結果が、今使っているギヤボックスを作るきっかけに成ってしまったのです。
最初の第1号機。ワウが酷かった。ギヤ同士の合わせ精度が低かった。
振動も多く、とても使い物に成らなかった。
でも、何とかしたい。カッティングマシンに負けたくない。
今現在、カッティングマシンと五分五分の闘いの様です(先ほどのお客様の言)。
ただし、ギヤボックスもどんどん進化中。
今日もこれから、モーターの支持方式を変える図面の製図。
勿論、今迄に買って戴いた方へのフィードバックも出来る方法で。
物の完成度を上げるには、長い時間が掛かります。
僕のプリアンプ。25年以上、回路は変わっていません。
でも最初の1号機と、今のプリ。丸っ切りグレードが違います。
作って、散々使って、初めて判る事って多いんですね。
このプリも、年中回路や真空管を変えていたら、今の完成度には成らなかったと思います。
ギヤボックスも、産声を上げて2年弱。
更なる完成度を目指して・・・・・・。
完
その問題を解決するには、プーリーの回転数を落とせば良い。
ハイ、いたって簡単です。モーターの回転数を減速するだけですから・・。
で、その減速機構。騒音は一切ご法度。此れが難しい。コクドベルトやギヤ、どちらも騒音が付きまとう。
糸で二段減速。
此れも散々考えたんだけど、糸のテンションの取り方が難しい。プーリーの精度も大変。
自分だけが使う前提で、コスト(工数)を無視すりゃ出来ない事は無いけど、お客様に出す時の価格は抑えたい。
しかも、使い方が非常にクリティカルでは、一般の音楽ファンには使いこなせない。
そうなんです。自分だけが使うのならどんな方法も有るんですが、市販をする。もの凄く縛られるのです。
何とか減速をしたい。ウジウジの数年間だったのです。
そんな折、あるお客様が・・・・・・。
『カッティングマシンを買った。ピンキーさんの糸ドライブよりも良い。』
こんな電話を頂いたんですね。
まあ、普通の人間なら、カッティングマシンには敵う筈も無いよなー。
って考えるんでしょうが、普通の人間ではないピンキー君。
『プツン。』
切れちゃった。永年のウジウジが溜まりに溜まっていたんですね。
早速、そのカッティングマシンを見せてもらう。
かなりの年代物。駆動方式はギヤドライブ。ギヤにはウォームを使っている。
で、そのギヤボックスとターンテーブルの結合に、ギヤの騒音とシャフトの位置のずれの逃げの為にゴムを使っている。
そうか、確かにウォームなら騒音は少ない。
ターンテーブルとのゴム結合が有るのなら、こちらにも勝算が・・・・・。
結果が、今使っているギヤボックスを作るきっかけに成ってしまったのです。
最初の第1号機。ワウが酷かった。ギヤ同士の合わせ精度が低かった。
振動も多く、とても使い物に成らなかった。
でも、何とかしたい。カッティングマシンに負けたくない。
今現在、カッティングマシンと五分五分の闘いの様です(先ほどのお客様の言)。
ただし、ギヤボックスもどんどん進化中。
今日もこれから、モーターの支持方式を変える図面の製図。
勿論、今迄に買って戴いた方へのフィードバックも出来る方法で。
物の完成度を上げるには、長い時間が掛かります。
僕のプリアンプ。25年以上、回路は変わっていません。
でも最初の1号機と、今のプリ。丸っ切りグレードが違います。
作って、散々使って、初めて判る事って多いんですね。
このプリも、年中回路や真空管を変えていたら、今の完成度には成らなかったと思います。
ギヤボックスも、産声を上げて2年弱。
更なる完成度を目指して・・・・・・。
完
昨日の写真。判りましたでしょうか?
上のフライホイールを外しますと、この様に成ります。
モーターメーカーから出ている純正のギヤボックスなんですね。
此れをモーターの上に直接付けますと、回転数が数分の1に減速できます。
つまり、その分プーリー径を大きく出来るのです。
プーリー径が大きければ、糸との接触距離が増え、スリップは激減。
僕の思惑通り行くかは、やってみなくちゃ判りません。
机上の理論で済ませるのが大嫌いな性分です。
他人のHPを覗いて、判った振りなんて僕には出来ません。
兎に角、減速分に見合ったプーリーを作り、更にフライホイールを追加すると言う構成です。
出来上がり廻して見ると・・・・・・・。
ギヤの騒音が大きい。そりゃースパーギヤの組み合わせですから仕方が有りません。
問題はプレーヤーから聞こえる騒音がスピーカーからも出てしまうか・・?
レコードに針を下ろします。
スピーカーからはギャーと言うギヤ鳴りが・・・・。
ハイ、失敗です。でも・・・・・。
ギヤ鳴りに埋もれながらも聞こえる音楽。
間違いなく良く成っている。
中域のエネルギー感が段違い。
ヤハリ、糸とプーリーはスリップをしていたのです。
此れで、次の方向は見えました。
プーリーの径を大きくし、糸のスリップを防ぐ。
でも、どの様な減速機構を作れば良いのか・・?
この実験の結果は、僕の心の底に深く仕舞い込まれたのです。
続く
軸受けの更なるフリクションの低減で、回転ムラの無くなったターンテーブル。
ここで感じた事は、糸とプーリー間のフリクションの少なさ。此処はある程度大きくないと拙い。
レコードの音の溝。一定ではないのはご承知の筈。
無音溝はフリクションが小さく、大音量やパルスの時には大きなフリクションが働きます。
この不安定なフリクションに対して、絶対に糸とプーリー間のスリップは起きてはいけないんですね。
糸のテンションを上げれば、ある程度は増えますが、プーリーと糸の寿命を考えますと、行いたく有りません。
僕のプレーヤーは、車に例えればレーサーではなくファミリーカーなのです。
短期間の高性能ではなく、長期の動作を保障したいんですね。
一番簡単な、プーリーと糸とのフリクションを上げるには・・・・・・。
プーリー径を大きくし、糸との触れる長さを長くすれば・・・・・・。
写真が其の実験でした。
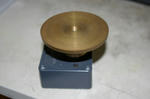

続く
ここで感じた事は、糸とプーリー間のフリクションの少なさ。此処はある程度大きくないと拙い。
レコードの音の溝。一定ではないのはご承知の筈。
無音溝はフリクションが小さく、大音量やパルスの時には大きなフリクションが働きます。
この不安定なフリクションに対して、絶対に糸とプーリー間のスリップは起きてはいけないんですね。
糸のテンションを上げれば、ある程度は増えますが、プーリーと糸の寿命を考えますと、行いたく有りません。
僕のプレーヤーは、車に例えればレーサーではなくファミリーカーなのです。
短期間の高性能ではなく、長期の動作を保障したいんですね。
一番簡単な、プーリーと糸とのフリクションを上げるには・・・・・・。
プーリー径を大きくし、糸との触れる長さを長くすれば・・・・・・。
写真が其の実験でした。
続く
長期の使用で、かじりを起こし、回転ムラを起こすターンテーブル軸受け。
モーターの回転数が高く、プーリー径が小さく、糸との接触面積が小さいのが一番の原因。
困りました。手でターンテーブルを廻しても、かじり等を手に感じないレベルなのです。
接触面で、一番摩擦抵抗が少ないのは点接触。只単位面積あたりの負荷は一番高い。
この負荷に耐える構造は・・・・・・・。
今のボールはシャフトと一緒に廻っている。
受けを平面ではなく球面にしたら・・・・・・・。
つまり、受け側にも鋼球を入れてしまうのです。
表面研磨は最高レベルですし、硬度も高い。
問題は、上のボールと下のボールのセンターを合わせる事。
量産品では難しいかもしれないけど、一個物の強み。
それと鋼球。球面です。センターが尖っている訳ではないので、若干の狂い(2~3/100mm)は平気な筈。
早速作って見ました。
今度は鋼球で受けるので、下の受けもアルミで平気。
しかも鋼球を固定する訳ではないので、分解する度に鋼球の向きが変わるので、磨耗しても平気。第一鋼球の値段は無茶苦茶安いし。
上下鋼球受けの軸受けが完成しました。
摩擦は最小。結果、糸の寿命が伸びたのです。
長期使用の鋼球をチェック。表面のオイルをふき取ると、当たった痕が見つからない。
つまり、磨耗をしていないのです。
この軸受けを採用して、ヤット軸受けの磨耗から開放されたのです。
続く
モーターの回転数が高く、プーリー径が小さく、糸との接触面積が小さいのが一番の原因。
困りました。手でターンテーブルを廻しても、かじり等を手に感じないレベルなのです。
接触面で、一番摩擦抵抗が少ないのは点接触。只単位面積あたりの負荷は一番高い。
この負荷に耐える構造は・・・・・・・。
今のボールはシャフトと一緒に廻っている。
受けを平面ではなく球面にしたら・・・・・・・。
つまり、受け側にも鋼球を入れてしまうのです。
表面研磨は最高レベルですし、硬度も高い。
問題は、上のボールと下のボールのセンターを合わせる事。
量産品では難しいかもしれないけど、一個物の強み。
それと鋼球。球面です。センターが尖っている訳ではないので、若干の狂い(2~3/100mm)は平気な筈。
早速作って見ました。
今度は鋼球で受けるので、下の受けもアルミで平気。
しかも鋼球を固定する訳ではないので、分解する度に鋼球の向きが変わるので、磨耗しても平気。第一鋼球の値段は無茶苦茶安いし。
上下鋼球受けの軸受けが完成しました。
摩擦は最小。結果、糸の寿命が伸びたのです。
長期使用の鋼球をチェック。表面のオイルをふき取ると、当たった痕が見つからない。
つまり、磨耗をしていないのです。
この軸受けを採用して、ヤット軸受けの磨耗から開放されたのです。
続く
ターンテーブルの軸受け部を、アイドラー時代の侭でのスタート。
アイドラー時代には何の問題も発生しませんでしたので、自信の軸受けだったのです。
シャフトは45C(炭素鋼)の削りだし。受けは青銅の削りだし。
スラスト加重は鋼球で受け、底部はやはり45Cで受けたのです。
一般の市販のターンテーブルと似た構造ですが、一工夫しました。
普通は鋼球は底部に固定。鋼球の上面とシャフトの底面が擦り合う仕組みです。
この構造ですと、最初に磨耗するのはシャフトの先端。シャフトの作り直しは大変(コストが掛かります)。
シャフトの先端にテーパー穴加工をし、此処へボールを固定(重量だけで固定できます)。ボールはシャフトと一緒に回る。
結果、磨耗は底蓋の45C。此れでしたら、磨耗して交換に成ってもコストが掛かりません。
機械物の設計で大切なのは、どちら側が先に磨耗させるかの考えです。将来の整備の時に、コストの掛からない方を先に磨耗させる設計が、巧いやり方です。
この状態で、長期の使用を始めました。
その内に回転ムラを始めたのです。
ほんの僅かですが、ピアノを聴くと・・・・・(ピアノは回転ムラに敏感です)。
原因を散々探しました。アイドラー時代には無かった現象です。
出た答えは、底蓋の45Cの磨耗。鋼球の当たった痕をルーペで拡大しますと、綺麗な磨耗ではなく、かじっているのです。
その結果、摩擦にムラが生じたのです。
アイドラーなら、駆動力が大きいので押し切ってしまうのでしょうが、糸の場合、プーリーと糸の接触面積は極少。
摩擦力の増減で、糸のスリップを誘発していると考えました。
受けを45Cから砲金に変えたり、鋼球との接触部分を研磨したり・・・。
色々とやっても最初は良いのですが、長期に使うと・・・・・・。
続く
アイドラー時代には何の問題も発生しませんでしたので、自信の軸受けだったのです。
シャフトは45C(炭素鋼)の削りだし。受けは青銅の削りだし。
スラスト加重は鋼球で受け、底部はやはり45Cで受けたのです。
一般の市販のターンテーブルと似た構造ですが、一工夫しました。
普通は鋼球は底部に固定。鋼球の上面とシャフトの底面が擦り合う仕組みです。
この構造ですと、最初に磨耗するのはシャフトの先端。シャフトの作り直しは大変(コストが掛かります)。
シャフトの先端にテーパー穴加工をし、此処へボールを固定(重量だけで固定できます)。ボールはシャフトと一緒に回る。
結果、磨耗は底蓋の45C。此れでしたら、磨耗して交換に成ってもコストが掛かりません。
機械物の設計で大切なのは、どちら側が先に磨耗させるかの考えです。将来の整備の時に、コストの掛からない方を先に磨耗させる設計が、巧いやり方です。
この状態で、長期の使用を始めました。
その内に回転ムラを始めたのです。
ほんの僅かですが、ピアノを聴くと・・・・・(ピアノは回転ムラに敏感です)。
原因を散々探しました。アイドラー時代には無かった現象です。
出た答えは、底蓋の45Cの磨耗。鋼球の当たった痕をルーペで拡大しますと、綺麗な磨耗ではなく、かじっているのです。
その結果、摩擦にムラが生じたのです。
アイドラーなら、駆動力が大きいので押し切ってしまうのでしょうが、糸の場合、プーリーと糸の接触面積は極少。
摩擦力の増減で、糸のスリップを誘発していると考えました。
受けを45Cから砲金に変えたり、鋼球との接触部分を研磨したり・・・。
色々とやっても最初は良いのですが、長期に使うと・・・・・・。
続く
チャンデバに掛かってから、更新の止まってしまったこのシリーズ。
意外な程、愛読者が多いので、僕も驚いて・・・・・。
暫らくぶりの再開です。
最初に出来上がった糸ドライブシステムは、従来のアイドラープレーヤーの外部に糸ドライブモーターをクランプするシステムでした。
要は、今迄のアイドラーを愛用していた方達へのグレードアップバージョンだったのです。
このシステム、従来のアイドラーの音をしのいではいたのですが、モーター振動をピックアップが拾い易い。
クランプのねじの締め具合などで逃げていたのですが、根本的な解決にはならず・・・・・・。
アイドラードライブの場合、メカがターンテーブルの下に集中していますので、プレーヤーキャビのくり貫き部分が多いのです。
つまり、キャビの強度、重量共に低下をしてしまうんですね。
まず、僕のプレーヤーで実験。
アイドラーのメカを全て取り外し、キャビもくり貫きの小さな物に作り変えたんですね。
糸ドライブのメカは一切変えずにです。
モーター振動がぐんと少なくなったのです。
キャビの強度と重量で、モーター振動を押さえつけたのです。
この辺から、アイドラーのグレードアップではなく、最初から糸ドライブでの設計の必要性を感じてきました。
結果、新しく作り直した糸ドライブシステムのプレーヤーが此れです。
http://hayashilab.syuriken.jp/aupureiya01.htm
ターンテーブルの軸受け部はアイドラーと共通でした。
此れが、長期の使用でトラブルを起こしたのです。
続く。
意外な程、愛読者が多いので、僕も驚いて・・・・・。
暫らくぶりの再開です。
最初に出来上がった糸ドライブシステムは、従来のアイドラープレーヤーの外部に糸ドライブモーターをクランプするシステムでした。
要は、今迄のアイドラーを愛用していた方達へのグレードアップバージョンだったのです。
このシステム、従来のアイドラーの音をしのいではいたのですが、モーター振動をピックアップが拾い易い。
クランプのねじの締め具合などで逃げていたのですが、根本的な解決にはならず・・・・・・。
アイドラードライブの場合、メカがターンテーブルの下に集中していますので、プレーヤーキャビのくり貫き部分が多いのです。
つまり、キャビの強度、重量共に低下をしてしまうんですね。
まず、僕のプレーヤーで実験。
アイドラーのメカを全て取り外し、キャビもくり貫きの小さな物に作り変えたんですね。
糸ドライブのメカは一切変えずにです。
モーター振動がぐんと少なくなったのです。
キャビの強度と重量で、モーター振動を押さえつけたのです。
この辺から、アイドラーのグレードアップではなく、最初から糸ドライブでの設計の必要性を感じてきました。
結果、新しく作り直した糸ドライブシステムのプレーヤーが此れです。
http://hayashilab.syuriken.jp/aupureiya01.htm
ターンテーブルの軸受け部はアイドラーと共通でした。
此れが、長期の使用でトラブルを起こしたのです。
続く。
実はこの仕事の最中に、アノ地震。
店は平気だったので、作業再開と思ったら、家から電話。
『家の中グチャグチャ。テレビは落ちるし、本やDVDも全て落ちたし、ピアノも危ない。家中、足の踏み場も無い状態・・・・・。』
慌てて、直ぐに帰宅。
この写真を撮っていたのも忘れていました。
今、写真を撮ってメモリーを見たら・・・・・。
完全に忘れていたんです(汗)
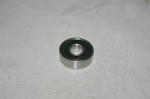
今回交換予定のベアリング。元々入っていた物と、基本的には同じです。シールの仕方が違うだけ。
元々入っているベアリングは、シールを外せません。
今回、ベアリングの音を小さくするのに、グリスを特殊なものに入れ替えようとの計画です。
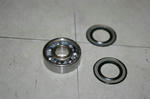
両側のシールを外し、内部のチェック。シリコン系と思われるグリスが入っています。
此れをパーツクリーナーで綺麗に洗浄。
で、この時の注意事項。ベアリングは凄く綺麗好きなのです。クリーンルームでしたい位綺麗好き。つまり微細なゴミもご法度。
手を綺麗に洗い、其れからの作業です。
で、この後の写真が有りません。慌てて帰ってしまったので・・・・。
ローターにベアリングを挿入中に地震が来たのです。
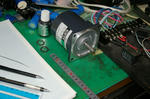
無事に回りだしたモーター。昨日の夕方から回っていますから、ソロソロ24時間。
今回使っているグリスは特殊でして、負荷が掛かると金属表面に特殊な処理をすると言う物です。
バイクの方のブログを見ている方ならハハ~~~ン。
実はその原液をギヤボックスの中のオイルにも混入。良い結果が出ましたので、其れが最初から混入してあるグリスへ詰め替えたのです。
と言う事は、直ぐには結果が出ません。
確かに、組んで直ぐと今では、騒音レベルが大分違います。
1週間ほど廻してから、ギヤボックスへ組み込みます。
で、モーターの傍らで、なにやら図面を・・・・・。
何の図面かはナイショ。以前から何とかしたかった事項を現実のものに・・。
結構難しい課題をクリアーしようとしています。
成功したら、僕の所の音は更に良くなる筈。勿論お客様へのフィードバックも考えています。
店は平気だったので、作業再開と思ったら、家から電話。
『家の中グチャグチャ。テレビは落ちるし、本やDVDも全て落ちたし、ピアノも危ない。家中、足の踏み場も無い状態・・・・・。』
慌てて、直ぐに帰宅。
この写真を撮っていたのも忘れていました。
今、写真を撮ってメモリーを見たら・・・・・。
完全に忘れていたんです(汗)
今回交換予定のベアリング。元々入っていた物と、基本的には同じです。シールの仕方が違うだけ。
元々入っているベアリングは、シールを外せません。
今回、ベアリングの音を小さくするのに、グリスを特殊なものに入れ替えようとの計画です。
両側のシールを外し、内部のチェック。シリコン系と思われるグリスが入っています。
此れをパーツクリーナーで綺麗に洗浄。
で、この時の注意事項。ベアリングは凄く綺麗好きなのです。クリーンルームでしたい位綺麗好き。つまり微細なゴミもご法度。
手を綺麗に洗い、其れからの作業です。
で、この後の写真が有りません。慌てて帰ってしまったので・・・・。
ローターにベアリングを挿入中に地震が来たのです。
無事に回りだしたモーター。昨日の夕方から回っていますから、ソロソロ24時間。
今回使っているグリスは特殊でして、負荷が掛かると金属表面に特殊な処理をすると言う物です。
バイクの方のブログを見ている方ならハハ~~~ン。
実はその原液をギヤボックスの中のオイルにも混入。良い結果が出ましたので、其れが最初から混入してあるグリスへ詰め替えたのです。
と言う事は、直ぐには結果が出ません。
確かに、組んで直ぐと今では、騒音レベルが大分違います。
1週間ほど廻してから、ギヤボックスへ組み込みます。
で、モーターの傍らで、なにやら図面を・・・・・。
何の図面かはナイショ。以前から何とかしたかった事項を現実のものに・・。
結構難しい課題をクリアーしようとしています。
成功したら、僕の所の音は更に良くなる筈。勿論お客様へのフィードバックも考えています。
さて、モーターは分解できました。
新しいベアリングの入荷待ち。
と言って休んでいる暇は無いのです。
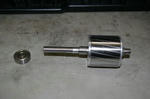
分解したモーターローターとベアリング。
シャフトの根元の光っている部分がベアリングの入っていた位置。
其処の左側は8mmに対して1/100mm程細くなっていて、ベアリングを挿入する部分は8mmピッタリです。
つまり細い部分はベアリングがスルスル入りますが、根元の部分は圧入が必要。
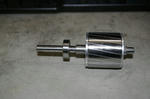
差し込みますと、此処の部分で止まってしまいます。
で、貴方ならどうします。
ベアリングを叩いたりしませんよね。
この場合、ベアリングに掛ける力はインナーレースだけに掛けて、間違ってもアウターを押してはいけません。
インナーに掛ける力も、周りを尖った棒でコツコツ叩いで・・・・。
斜めに力が加わりますからNGです。
で、こんな圧入器具を作りました。
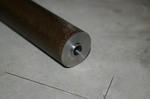
材質は鉄としては硬い部類に入る45C。インナーだけを押す為に、インナーの部分だけ1mm弱出っ張っています。
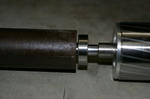
こんな感じですね。
で、作る時に困ったのが穴掘り。シャフトの長さ分必要。8,05mmのドリルが有ると一発なんですが、持っている8,05はショートタイプ。精度の高い穴を開けるには、ドリルは必要最低限の長さを選びます。
長さが足りないので、とりあえず8mmのドリル(コイツはロングを持っている)で、開けて見たけど、シャフトとのクリアランスが足りず、入ってくれない。
さて、此れだけの為にロングドリルを買うのも癪だし、ドリルの入荷まで作業は中断。
仕方が無い。面倒だけど穴ぐりバイトでほんの僅か穴を広げたんです。
明日、ベアリングは入荷しますから、明日中にはモーターが回るかも?
で、このモーター。ベアリングの支持方式にも問題が有ったりして・・・。
新しいベアリングの入荷待ち。
と言って休んでいる暇は無いのです。
分解したモーターローターとベアリング。
シャフトの根元の光っている部分がベアリングの入っていた位置。
其処の左側は8mmに対して1/100mm程細くなっていて、ベアリングを挿入する部分は8mmピッタリです。
つまり細い部分はベアリングがスルスル入りますが、根元の部分は圧入が必要。
差し込みますと、此処の部分で止まってしまいます。
で、貴方ならどうします。
ベアリングを叩いたりしませんよね。
この場合、ベアリングに掛ける力はインナーレースだけに掛けて、間違ってもアウターを押してはいけません。
インナーに掛ける力も、周りを尖った棒でコツコツ叩いで・・・・。
斜めに力が加わりますからNGです。
で、こんな圧入器具を作りました。
材質は鉄としては硬い部類に入る45C。インナーだけを押す為に、インナーの部分だけ1mm弱出っ張っています。
こんな感じですね。
で、作る時に困ったのが穴掘り。シャフトの長さ分必要。8,05mmのドリルが有ると一発なんですが、持っている8,05はショートタイプ。精度の高い穴を開けるには、ドリルは必要最低限の長さを選びます。
長さが足りないので、とりあえず8mmのドリル(コイツはロングを持っている)で、開けて見たけど、シャフトとのクリアランスが足りず、入ってくれない。
さて、此れだけの為にロングドリルを買うのも癪だし、ドリルの入荷まで作業は中断。
仕方が無い。面倒だけど穴ぐりバイトでほんの僅か穴を広げたんです。
明日、ベアリングは入荷しますから、明日中にはモーターが回るかも?
で、このモーター。ベアリングの支持方式にも問題が有ったりして・・・。