ベアリング内臓のグリスの種類を変えて、ベアリングノイズを減らす作戦。
見事に轟沈。
ハイ、失敗は最高の教科書です。
失敗の原因、ベアリングをシャフトに挿入。此れは専用の打ち込み工具を作ったので問題無い。
問題は、モーター本体への組み込み。
このモーター、上部の蓋と本体底にベアリングが入ります。
蓋と本体の接合。ネジでの接合なら問題は無かったのですが・・・・。
蓋の挿入部分テーパー加工。本体もテーパー受け。確かにこの方法ならセンターを出すのは確実です。
問題は組み立て方法。圧入。この時、モーターとベアリングの隙間がタップリ有れば問題無んいですが、そんな事をしたらモーターはまともに回らりません。
ギリギリの隙間。圧入の時、蓋が完全に本体に真っ直ぐなら良いのですが・・・。
若干、傾くとベアリングに応力が・・・。
結果、レースに打痕を・・。
僕も此の辺は理解していたので、可也注意深く打ち込んでいたのです。
で、理解出来ました。メーカー組み込み時にも僅かながら打痕をつけている恐れ大。
今時のベアリングにしては、ベアリングノイズが大き過ぎます。打痕がついてるとしたら・・・・・・。
実際に、ノイズ量に当たり外れが有りますし・・・。
つまり、この方式ではベアリングノイズを消すのは難しいのです。
其処で次の方法。プレーンベアリング。要はメタル。
と言っても金属は使いません。エンプラです。MCナイロンに潤滑剤を封入した物です。
とりあえず、精密ドリルで孔を開けて見ました。
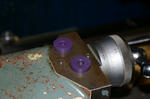
樹脂は、金属と較べると、機械強度(大きな応力には強いのですが、僅かの応力での変形に弱い)に劣ります。
結果刃から僅かに逃げるんですね。ほんの少しですが小さな穴に成ってしまいました。
シャフトは入るのですが回すとキツイ。
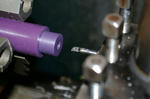
その様な時は面倒ですが穴グリバイト。欲しい穴より小さ目のドリルで下穴加工。其の後このバイトで穴を拡げるのです。
この時成功させるコツは、急がない。
エーイ面倒也、と一気に拡げると、大き過ぎる穴を開けて最初から。急がば廻れです。
見事に成功。
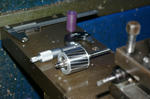
モーターシャフトを何度も押し当てて確認。
最初は0,1mmバイトを動かしますが、目標の寸法に近づいて来たら、0,025mm。其の後0.01mm(此の辺は感覚)。
最後は、バイトの位置を変えずに再切削。穴グリの場合、バイトの位置を変えないで二度切削しますと、わずかながら削れるんですね。
量産品にはとても出来ない方法ですが、趣味ですので・・(笑)。
見事に轟沈。
ハイ、失敗は最高の教科書です。
失敗の原因、ベアリングをシャフトに挿入。此れは専用の打ち込み工具を作ったので問題無い。
問題は、モーター本体への組み込み。
このモーター、上部の蓋と本体底にベアリングが入ります。
蓋と本体の接合。ネジでの接合なら問題は無かったのですが・・・・。
蓋の挿入部分テーパー加工。本体もテーパー受け。確かにこの方法ならセンターを出すのは確実です。
問題は組み立て方法。圧入。この時、モーターとベアリングの隙間がタップリ有れば問題無んいですが、そんな事をしたらモーターはまともに回らりません。
ギリギリの隙間。圧入の時、蓋が完全に本体に真っ直ぐなら良いのですが・・・。
若干、傾くとベアリングに応力が・・・。
結果、レースに打痕を・・。
僕も此の辺は理解していたので、可也注意深く打ち込んでいたのです。
で、理解出来ました。メーカー組み込み時にも僅かながら打痕をつけている恐れ大。
今時のベアリングにしては、ベアリングノイズが大き過ぎます。打痕がついてるとしたら・・・・・・。
実際に、ノイズ量に当たり外れが有りますし・・・。
つまり、この方式ではベアリングノイズを消すのは難しいのです。
其処で次の方法。プレーンベアリング。要はメタル。
と言っても金属は使いません。エンプラです。MCナイロンに潤滑剤を封入した物です。
とりあえず、精密ドリルで孔を開けて見ました。
樹脂は、金属と較べると、機械強度(大きな応力には強いのですが、僅かの応力での変形に弱い)に劣ります。
結果刃から僅かに逃げるんですね。ほんの少しですが小さな穴に成ってしまいました。
シャフトは入るのですが回すとキツイ。
その様な時は面倒ですが穴グリバイト。欲しい穴より小さ目のドリルで下穴加工。其の後このバイトで穴を拡げるのです。
この時成功させるコツは、急がない。
エーイ面倒也、と一気に拡げると、大き過ぎる穴を開けて最初から。急がば廻れです。
見事に成功。
モーターシャフトを何度も押し当てて確認。
最初は0,1mmバイトを動かしますが、目標の寸法に近づいて来たら、0,025mm。其の後0.01mm(此の辺は感覚)。
最後は、バイトの位置を変えずに再切削。穴グリの場合、バイトの位置を変えないで二度切削しますと、わずかながら削れるんですね。
量産品にはとても出来ない方法ですが、趣味ですので・・(笑)。
この記事のトラックバックURL
この記事へのトラックバック