昨夕、運転を開始したギヤボックス。 今迄の軸受けでしたら、回した侭で帰ったのですが、今回は初めての樹脂軸受け。 熱膨張が怖いのです。夜中に止まったら・・・・(汗)。 と言う事で、昨日の運転はほんの1時間。 今朝は出勤と同時に運転開始。もうそろそろ6時間を迎えます。 ウォーギヤですので、歯車は擦動運動。研磨をして有るギヤですが、それでも最初の3時間でオイルは結構汚れます。 しかも金属粉で。 4時間辺りで最初のオイル交換。機械物を長持ちさせたければ、オイル交換はマメに。 勿論、試運転中にも僕には仕事が・・。 最後のパーツ。プーリーの切削です。内部にワンウェイクラッチを仕込みますので、穴径の精度は2/100以下の誤差。 明日には納品できるかな? PM5:00。追記です。 たった今、店のプレーヤーに接続。これ納品したくないなー(汗)。
ヤット、ギヤボックスの組み立てが始まりました。
一番重要な組立工程。ギヤボックスとモーターのシャフトを、如何に直線上にするか。
此処の僅かなズレが、騒音の元凶に成るのです。
間に差し込んで有るのは、位置出しの冶具。要はアルミにシャフト径の穴を開けただけ。
カップリングには必要なガタが有るので、シビアな位置合わせは出来ません。
ガタの無いアルミでスルッと動く様にしないと駄目なんですね。
冗談ではなく、このギヤボックス。ユーザーの方が緩めて良いのは、オイルのドレンとフィラーのみ。
それ以外のボルトに緩めた形跡がある場合は、クレーム対象に成りません。
その位、シビアな位置出しをしています。
写真のボルト。一般のM5へ二次加工がして有ります。
写真で直ぐに判りますよね。ネジ部に下から穴を開け、天井に抜ける前に寸止め。
六角部の横から、下から開けた穴と貫通穴を。
下からの穴は旋盤。横穴はフライス盤で加工。
一般の機械屋さん。以前にも書きましたが、旋盤屋さんとフライス盤屋さんとに別れているのが普通。
この様な加工の時には、二箇所を持ち回り。
ばかばかしい程時間が掛かります。
手持ちの工作機械が、あればあっと言う間(と言っても結構面倒なんですが)。
で、このボルト。何に使うの?
ブリザーと言う言葉知ってます?
バイクや車のエンジンに必ず必要なパーツ。
今回のギヤボックスの場合で考えて見ましょう。
オイルが漏れてはいけませんので、基本的に密閉です。
で、この密閉が危ない。
連続運転中は温度が上がりますし、冬の夜中には・・・・・。
そうなんですね。温度変化に対応しないと拙いのです。
温度が上がれば内部の空気が膨張しますし、冷えると逆。
此れを密閉で抑えるのは無理なんですね。
で、ギヤボックスの一部に小さな穴を開けて、外部の空気と繋がないと拙いのです。
その働きをさせるのが写真のボルト。
ギヤボックスの一部に取り付け、外部と繋ぎます。
オイルが吹いたり、外部のごみを吸ったりしない事が条件。
勿論、此れは今迄に作ったギヤボックスにも取り付けて有りますよ。
完成の近付いたギヤボックス。
周りのケースの精度に、細心の注意を払うのは当然ですが・・・・。
写真のギヤ。主人公のギヤです。10:1に減速します。少しでもノイズを減らす為に研磨ギヤを使っています。
で、問題。左右のギヤ、違い判りますよね。
穴径が違うのですね。
なんだそれだけか。なんて思わないで下さい。
メーカーから購入したギヤには6mmの穴が開いています。それを8mmに広げるのです。
単に広げるだけでしたら、ボール盤でも出来ますが・・・・・。
ギヤに対するセンター、直角度を守らないといけないんですね。
旋盤で加工すれば簡単ですか?
旋盤って、そんなに当てに出来る精度じゃ無いんですね。
精度を出したければ、一度チャックに銜えた工作物は、外さないでの加工が基準です。
メーカーで削った歯車を、此処の旋盤でも同じ様に精度を出してチャックに銜える。
さあ、どうしましょう。
こんな方法、だれも教えてくれません。
実際に1号機のギヤボックス。此処の精度が出なかった為に、ピアノが聴けませんでした。
若干のワウ。他の楽器は誤魔化せてもピアノは誤魔化せない。
ギヤを何個も買って(高いんですよー)切削の方法を変えてみる。
旋盤を購入した当時でしたら、絶対に加工不可能でした。
色々と経験したからこそ、出来た加工と思っています。
今回も慎重に加工。巧く行きました。シャフトと穴のクリアランス。1/100以下です。
今回受注したギヤボックス。チョットのマイナーチェンジ。
軸受けを変更したのです。
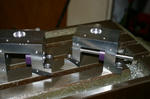
2個作っていますが、1個は僕の分(笑)。まさか変更品のテストを、お客様だけにやってもらう訳には行きませんから。
正直に言いますと、今僕の使っている物。大外れ。原因は今一判っていないのですが騒音が大きい。
自分で使うのなら我慢しますが、お客様には渡せない代物です。
注文が入ったと同時に自分の物も・・・・(職権乱用)。
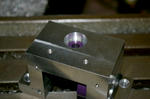
まず立てシャフトの出力部分。此処は糸の張力で、横へ力が掛かります。一番磨耗の心配な部分なんですね。と言っても、磨耗した物は未だに出ていませんが。
で、今迄此処へは市販の軸受けを使用していました。産業用ですので耐久力は大丈夫と思うのですが、万が一磨耗すると交換が大変。高圧入なのです。
其処で、最近手馴れてきたエンプラで軸受けを作りました。作る分手間は大変ですが、長い使用を考えての変更です。

もう一箇所。此処は以前リコール対策した部分。
エンプラのカラーを入れて対策したのですね。
今回、このカラーと軸受けの一体化を計ったのです。
こうするとカラーの回転は防げますし、軸受けの交換も楽に成ります。
問題は、これからの長期使用でどう成るか?
正直、自信は有ります。
そうでなかったら、お客様へ最初からの採用は出来ません。まあ古くからの友人でも有るので、気楽に・・・・・(笑)。
勿論、今迄のギヤボックスを、この軸受けへの変更も出来る様に考えています。
騒音も減る筈ですので。
軸受けを変更したのです。
2個作っていますが、1個は僕の分(笑)。まさか変更品のテストを、お客様だけにやってもらう訳には行きませんから。
正直に言いますと、今僕の使っている物。大外れ。原因は今一判っていないのですが騒音が大きい。
自分で使うのなら我慢しますが、お客様には渡せない代物です。
注文が入ったと同時に自分の物も・・・・(職権乱用)。
まず立てシャフトの出力部分。此処は糸の張力で、横へ力が掛かります。一番磨耗の心配な部分なんですね。と言っても、磨耗した物は未だに出ていませんが。
で、今迄此処へは市販の軸受けを使用していました。産業用ですので耐久力は大丈夫と思うのですが、万が一磨耗すると交換が大変。高圧入なのです。
其処で、最近手馴れてきたエンプラで軸受けを作りました。作る分手間は大変ですが、長い使用を考えての変更です。
もう一箇所。此処は以前リコール対策した部分。
エンプラのカラーを入れて対策したのですね。
今回、このカラーと軸受けの一体化を計ったのです。
こうするとカラーの回転は防げますし、軸受けの交換も楽に成ります。
問題は、これからの長期使用でどう成るか?
正直、自信は有ります。
そうでなかったら、お客様へ最初からの採用は出来ません。まあ古くからの友人でも有るので、気楽に・・・・・(笑)。
勿論、今迄のギヤボックスを、この軸受けへの変更も出来る様に考えています。
騒音も減る筈ですので。
ボチボチと始まりました、ギヤボックスの製作。
4個のアルミブロック。2台分の材料です。
購入するアルミブロック。二面間の平行度だけ信用でき、それ以外は全然信用出来ない精度です。
此れを6面全ての制度(直角度、表裏の平行度、各面のサイズ)を出しませんと、この後の切削精度は保障出来ません。
何事も下準備なんですね。
兎に角、こんな切削。切削時間よりもフライスの掃除の方が大変。切削屑(切り粉)を挟んでしまうと、その分精度が狂うのです。
材料の向きを変える度に、兎に角掃除。
更に上下のブロックの厚み。上下に掛かってアクリル板でオイルを抑えますので、厚みの誤差を最小にしないとオイル漏れが待っています。
つまり上下の厚み切削は、セッティングを弄らないでの切削をしないとオーマイゴット。
今回の2組の材料。4個とも同じ厚みに合わせていますので、どちらの材料と組み合わせても大丈夫。
この様な単純な形でも、切削順序を間違えると、精度が出ません。頭がスッキリしていないと無理なんです。
今日は今一の頭の状態。此れは体調を崩す前に削り終えています。続きは体調を完璧にしてからですね。
暫らくぶりに、ギヤボックスの製作です。要は先日作ったQRKの軸受け。あそこまで作るとアイドラードライブは無理(笑)。
最初から、糸ドライブへの変更が前提での軸受けだったのです。
ギヤボックスのケースの材料。6000番台のアルミ板。
板とは言えないですね。50mm厚ですので・・。
まあ、アルミのブロックです。
上下2分割ですから、上下の板厚は完全に合わせませんと、オイル漏れを起こします。
図面上の板厚50mm。
前回買った板は、50mmに若干足りなく(公差範囲)、図面を49mmで引き直しました。
今回の板、50mmを超えています。
思わずニコッ。
此れを50mmに仕上げるのは簡単。
この位の削り代が、丁度やり易い寸法です。
昼食後、50mmに仕上げますか。