ギヤボックス君。頭を下げて謝ってます。
お漏らしをした小学生の様。
今朝出勤後、一番の確認。オイル漏れ。
やってましたねー。シッカリと。
手持ちの関係で、ソフトのソルボセインを使ってしまいましたので、一抹の不安は有りました。
さてどうするか?
ハードのソルボセイン(色を黒)は特注品。
納期に2~3週間掛かる。
ノンビリ待つのも手ですけど・・・・・・。
で、こんな時、バイクを弄っていると色々なアイディアが・・・・・。
ガスケットシート、あそこのバイク用品店で売ってないかな?
実は、ソルボセインを剥がし、工作用紙を挟んで見たら、中々良い感じ。
問題は、工作用紙ではオイルが染み込んで汚らしい。耐久性にも問題有るし・・。
早速二輪用品店。シッカリとガスケット紙を売っていた。取り寄せだったら時間が掛かって大変だったんだけど。
さて、これなら専門の用紙。漏れないだろうね・・・・?
ヤット、ギヤボックスにオイルを注入できました。
エッ、組んでからではないの?
そう、確かにこの状態でオイルを注入してしまうと、この後の組み立てはとてもやり辛い。
でも、これは有る意味試作機2号。
最初の試作機は、兎に角ギヤで減速、その後糸ドライブと言う、プロセスが正しいか、また巧く動作するかの確認の為の試作機です。
確かに、再生音は狙った通りのグレードアップ。
で、其の侭で作ればOKと言うほど物作りは甘くない。
長時間使っていると、色々な問題が露呈。
一番の問題は、オイルの排出がやり難い。ウォームギヤはオイルの傷みが激しいとは聞いていましたが、これ程とは・・。
オイル交換は結構頻繁に必要。
そう成ると、オイル交換が容易く出来る様に、構造変更です。
更に問題。液体パッキンがアクリルから剥がれない。
液体パッキンの性質に、剥がれ易い。と言う項目が有ります。
これはメンテの時に重要な項目。くっついた侭ですと、次の組み立てが出来ません。
メンテが一切要らないと言うなら、OKですがそうは行きません。
アルミからは綺麗に剥がれるのですが、アクリルには完全に溶着状態。
一度メンテで剥がし、もう一度液体パッキンを使うと、オイル漏れが発生しました。
メンテの度に、アクリル板交換では、コストが掛かってしまいます。
新しく、ゴムパッキンを使う事にしました。それもソルボセイン。耐油で振動を抑える好材料です。
ゴムを使ったもう一つの理由。
アクリルのネジ穴にクラックが入ってしまうのです。
数枚駄目にしました。強度の高いアルミブロックへの直接の取り付けは難しい様です。
まあ、内部の寸法変更は可也のもの。特に軸受けメタルを圧入する下穴寸法は1/100での調整が必要でした。
出来上がった物を見ただけでは判らない、製作者の苦労です。
で、最初の問題。なんでこの状態でオイルを入れたか?
オイル漏れの確認です。
この侭一昼夜放置。にじみが無ければ成功です。
注残を抱えた侭のギヤボックス。
流石に試作機と違い、納める商品ですから、気遣います。
第一、試作機には電源SWも付いていなかったのですから(汗)。
モーターシャフトとギヤボックスシャフトを繋ぐカップリング。
此処もむき出し状態。コリャー拙い。
カップリングのカバーを作り、其処に電源Swを付け、内部には進相コンデンサーを入れ、感電事故も防がねければいけないし。
図面の引き直し、何枚書いたかな。
更に試作機を長時間(2週間程ですが)運転したら、大事な事が持ち上がった。
カップリングのセンターだし。本当に微妙だがカップリングにも馴染みが出て来た。
調整をしなおせば良いのだけれど、ユーザーレベルでは絶対に無理。
今回のギヤボックス。ユーザーにはオイル交換以外はしてもらいたくない。
特に、カップリングの位置調整は絶対にNG。
オーナー自身でカップリングの位置調整をやってしまったら、一切のアフターを断るつもり。
そのくらい微妙な所なんです。
一台目は今週中に完成予定。でも、エージングが有るので、納めるのはいつかな?
今朝の僕の作業机の上。
出来上がっているギヤボックス。手で廻して見ると、試作機よりも軽く廻る。ガタもないし。
で、作業中断。
両側のアクリル板が出来てこない。イエ板は有るんですが、欲張ってロゴを入れたくなった。
ロゴの型は出来たので、ロゴ第一号になるギヤボックス。
今朝も、別の用事でロゴの彫刻を頼んでいる彫刻屋さんへ行って来た。
未だ、出来上がっていない。と言うか掛かってもいない。
社長の話。『どういう方法で彫るか考え中なんですよ。』
僕も物を作る立場。この言葉の意味、痛いほど分かる。
物を作るにしても、手順が色々考えられる。で、この手順。ものすごく大事。これで出来上がった物の出来具合、天と地の差が出る。
僕も初めての物を作る時、この手順を嫌と言う程考える。
勿論一号機を作りながら、次回はこの方法が良いかな?も考えているし。
チョットした順番の違いで、出来上がり精度や作業時間に差が出来てしまうのだから仕方が無い。
今度のロゴの彫刻。彼にとって初めての字体。
どういう手順で彫るのが一番綺麗か考えての事。
さっさとやっつけ仕事でやってしまうような所には、僕の仕事は出したくない。
どんな物もそう。最初の一つ。すごいエネルギーが必要なんです。
上下二分割のギヤボックス本体。
1号機とは、細かな所がかなり違っています。
と言う事は、このギヤボックスも、ある意味試作機。
つまりこの様な物は、作って見ないと判らない事が沢山。
インターネットなんかで調べたって正しい答えなんか見つかりっこない。
前回と違う工作をした所の確認が大切。
これをしないで出荷なんてしたら結局自分に帰ってくる。
本組みの前に仮組みをしました。
変換点の内の一つ。軸受けの穴のサイズを微妙に変えました。
仮組みでは良い感じ。ウン、今度の方が動きが軽いな。
動きが軽ければ、モーターに加える電圧を下げる事が出来ます。
結果、モーターの振動が減り、更に静かに。
これから本組み。
上下の位置関係をシッカリと固定。これが出来ないとシャフトの廻り方が重くなります。
で、問題は、中にはオイルを入れる。
接合部からオイルが漏れたら昔のオートバイ。
ペーパーガスケットは使いません。
ガスケット分、寸法が狂うのを避けるためです。
でも、何かしらの漏れ止めは必要。
此処で使うのが液体ガスケット。微細な厚みで漏れを防いでくれます。
只今、万力に挟んで、ガスケットの乾燥待ち。
こんな方法を思いつくのも普段の行い(笑)。
芸が身を助ける、と言うでは有りませんか。
ですから、僕のバイク弄り、邪魔しちゃ駄目ですよ。
それなりに成功を収めたギヤボックス。
試作品は店の中で廻しっぱなし。
納めてからのトラブルは避けたい。
で、若干の問題点。モーター部から時々ゴトゴト音。
出たり出なかったり。
原因は判っています。モーターとギヤボックスを繋いでいるカップリング。
兎に角指定が煩い。0.1mm以下の誤差での取り付けを要求。
そのくせ、両側のセンターが合っているかと言うと、角度的に?
まあ、使っているうちに馴染むだろう。
なんせ、初めて使う部品へ、短期に結論を出すのはご法度。
暫く様子を見ていたが、減る気配は更々無し。
ウーーン。もう一度位置出しをするか。
今度はお互いのシャフトを差し込む冶具(アルミの丸棒に8mmの穴を開けた物)を作った。
冶具ですから、穴の精度は1/100で管理。ドリルでの穴あけでなく、旋盤仕上げ。
此れで位置出しをすれば完璧。
もう一度モーター取り付けネジを緩め、真剣に位置を出す。
ヤハリ若干狂っていた。
シビアに合わせると、シャフトの廻りが軽い。
ハハハ。早く作れば良かった(まあ、この方法を考え付かなかったんですけど、汗)。
で、此処からが問題。
軽く廻る位置を見つけた。
其処で、モーター取り付けステーの止めネジを締める。
回転が重くなる・・・・・・。
弛めると軽くなる。でもその状態でモーターを廻したらすごい振動。
もう判っちゃいましたよね。
モーター取り付けステーの取り付け面(下面)の平面が出ていない。
早速、在庫の取り付けステーを、ガラスの上に置いたサンドペーパーで磨くと・・・・。
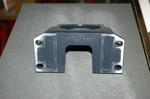
あのさー。お宅の会社でカップリングも出してるんだよね。
カップリングの取り付け誤差。無茶苦茶ウルサイよね。
で、取り付けステーの精度が出ていないって何なの?
まあ、メーカーってこんなもんです。大メーカーほど危ない。
削るか・・・・・。
その後、数十分・・。
研磨の終わったステーと今迄のを交換。
こんなもんですね。カップリングからの音は消滅。
モーター音とギヤ音のシャーと言うノイズのみ。
勿論、スピーカーからはその音は出ません。
で、再生音。
更に良く成りました。
低域の弾みが気持ち良い。
さて、量産量産。
試作品は店の中で廻しっぱなし。
納めてからのトラブルは避けたい。
で、若干の問題点。モーター部から時々ゴトゴト音。
出たり出なかったり。
原因は判っています。モーターとギヤボックスを繋いでいるカップリング。
兎に角指定が煩い。0.1mm以下の誤差での取り付けを要求。
そのくせ、両側のセンターが合っているかと言うと、角度的に?
まあ、使っているうちに馴染むだろう。
なんせ、初めて使う部品へ、短期に結論を出すのはご法度。
暫く様子を見ていたが、減る気配は更々無し。
ウーーン。もう一度位置出しをするか。
今度はお互いのシャフトを差し込む冶具(アルミの丸棒に8mmの穴を開けた物)を作った。
冶具ですから、穴の精度は1/100で管理。ドリルでの穴あけでなく、旋盤仕上げ。
此れで位置出しをすれば完璧。
もう一度モーター取り付けネジを緩め、真剣に位置を出す。
ヤハリ若干狂っていた。
シビアに合わせると、シャフトの廻りが軽い。
ハハハ。早く作れば良かった(まあ、この方法を考え付かなかったんですけど、汗)。
で、此処からが問題。
軽く廻る位置を見つけた。
其処で、モーター取り付けステーの止めネジを締める。
回転が重くなる・・・・・・。
弛めると軽くなる。でもその状態でモーターを廻したらすごい振動。
もう判っちゃいましたよね。
モーター取り付けステーの取り付け面(下面)の平面が出ていない。
早速、在庫の取り付けステーを、ガラスの上に置いたサンドペーパーで磨くと・・・・。
あのさー。お宅の会社でカップリングも出してるんだよね。
カップリングの取り付け誤差。無茶苦茶ウルサイよね。
で、取り付けステーの精度が出ていないって何なの?
まあ、メーカーってこんなもんです。大メーカーほど危ない。
削るか・・・・・。
その後、数十分・・。
研磨の終わったステーと今迄のを交換。
こんなもんですね。カップリングからの音は消滅。
モーター音とギヤ音のシャーと言うノイズのみ。
勿論、スピーカーからはその音は出ません。
で、再生音。
更に良く成りました。
低域の弾みが気持ち良い。
さて、量産量産。
世の中は10連休だ。16連休だって騒いでいるのに、一人がんばっています。
調子に乗って、ギヤボックス。沢山の人(と言っても10人ぐらいかな?)に聞かせ過ぎ。
現在受注6台。
全て手作りですから大変なのです。
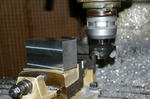
とりあえず、材料は4台分ゲット。
単なるアルミの塊から、キッチリした寸法に削り出します。
此処で、手を抜くと後々の精度が出ません。
試作機で使ったエンドミルは、精度を出すのにチョット苦労。
切削刃を替えました。
写真に写っている刃の方が、精度、表面の艶、共に上出来です。
最初から使えばよかった。なんせ試作機は何が起こるか判らない。
一気に削るのが怖かったのですね。
ギヤボックスの本体は上下二分割。其々に軸受けが有って、そのセンターを出さないと回転に無理が掛かります。
面倒ですが、上下一対での切削。と言う事は間違えて組み合わせたらオーマイゴット。
オッチョコチョイの僕の事ですから十分に考えられる。
で、いっぺんに6台は作らないで、二台ずつ。此れなら間違えないかな?
調子に乗って、ギヤボックス。沢山の人(と言っても10人ぐらいかな?)に聞かせ過ぎ。
現在受注6台。
全て手作りですから大変なのです。
とりあえず、材料は4台分ゲット。
単なるアルミの塊から、キッチリした寸法に削り出します。
此処で、手を抜くと後々の精度が出ません。
試作機で使ったエンドミルは、精度を出すのにチョット苦労。
切削刃を替えました。
写真に写っている刃の方が、精度、表面の艶、共に上出来です。
最初から使えばよかった。なんせ試作機は何が起こるか判らない。
一気に削るのが怖かったのですね。
ギヤボックスの本体は上下二分割。其々に軸受けが有って、そのセンターを出さないと回転に無理が掛かります。
面倒ですが、上下一対での切削。と言う事は間違えて組み合わせたらオーマイゴット。
オッチョコチョイの僕の事ですから十分に考えられる。
で、いっぺんに6台は作らないで、二台ずつ。此れなら間違えないかな?